Dlaczego Carbon Fiber jest materiałem cud
Stronger niż stal i ułamek masy, włókno węglowe jest genialny wynalazek. Był przez dziesięciolecia. Już w latach 80. Junior Johnson budował z niego łamiące zasady wyścigi Nascar. Ale nawet po upływie tego czasu, kiedy wymyślono nowe źródła zaopatrzenia i metody produkcji, włókno węglowe nie przestaje być drogie. Najtańszy nowy samochód z karbonową karoserią, Alfa Romeo 4C, jest wielkości Stuarta Małego, ale kosztuje tyle, co Mercedes klasy E. A prawdziwe rydwany karbonowych bogów, McLareny, Koenigseggeny i Lamborghini Aventadory, to już w ogóle sześciocyfrowe propozycje. Nadal nie udało nam się wyprodukować tego materiału na skalę masową w cenie zbliżonej do aluminium, nie mówiąc już o stali. Dlaczego nikt nie wpadł na to, jak sprawić, by te rzeczy kosztowały mniej?
To pytanie jest dlaczego jestem tutaj w Sant’Agata Bolognese, Włochy, w zakładzie Lamborghini z włókna węglowego, pracowicie wyciskając pęcherzyki powietrza z arkusza splotu węgla. Chciałbym zapytać facetów w (czarnych) fartuchach laboratoryjnych, którzy wytwarzają ten materiał: Dlaczego nie jeździmy Hyundaiami z karbonowym kokonem?
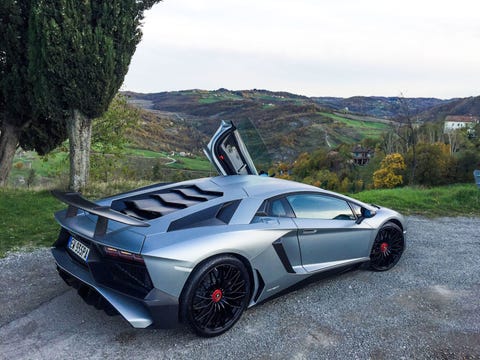
Carbon vs. Steel
W 2017 roku, aby stworzyć metalowe komponenty stanowiące rdzeń większości samochodów, wlewasz swoje supergorące płynne aluminium lub stal albo magnez do formy i odlewasz. Możesz rozbić go do kształtu, możesz wyrzeźbić go za pomocą maszyny CNC, możesz spawać kawałki razem. Masz opcje, wszystkie z nich są dość szybkie i niedrogie. Aby zrobić część z włókna węglowego … cóż, najpierw musisz wyjąć surowiec z zamrażarki.
Błyszczące, tkane rolki włókna węglowego, wypełnione żywicą (zwaną pre-preg) i pokryte klejem, są przechowywane w temperaturze 0 stopni Fahrenheita. Jeśli będzie cieplej, żywica stwardnieje. Ta wrażliwość na temperaturę oznacza również, że nie można ciąć materiału laserem CNC – aby zachować jego niską temperaturę i plastyczność, trzeba użyć ostrza, które w końcu się zużywa. Nawet wtedy zegar tyka. Od momentu przecięcia pierwszego splotu tych plastikowych nici węglowych, masz około jednego dnia na nadanie im kształtu.
Śpieszysz się więc z plastikowymi szpatułkami i wtłaczasz czarne i srebrne arkusze do formy, która będzie dobra tylko na około 300 użyć, zanim się zdeformuje i zostanie wyrzucona. Piera, kobieta, której zadaniem jest wytłumaczenie mi tego wszystkiego, wydaje się być zdumiona moim powolnym tempem. Podaje suszarkę do włosów i podgrzewa materiał, aby stał się bardziej elastyczny. Ale oczywiście, nie chcesz za dużo ciepła, żeby twój pre-preg nie zwapniał przedwcześnie w niewłaściwy kształt.
Futurystyczne, ale wykonane ręcznie
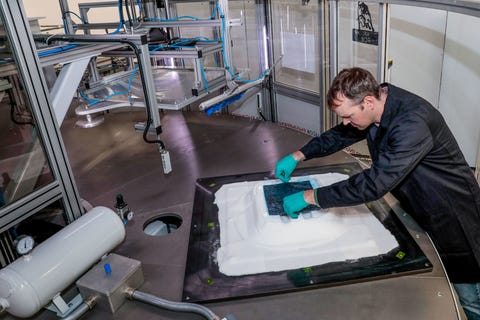
Około dekady temu odwiedziłem inną z fabryk Lamborghini. Obserwowałem, jak kobieta z miłością zszywała siedzenia w Murciélago, praktykując metodyczne rzemiosło, które byłoby zbyt pracochłonne, zbyt nieefektywne dla samochodu przeznaczonego na rynek masowy. Teraz znów jestem świadkiem podobnego stopnia ręcznego kunsztu włożonego w tworzenie materiału, który uważamy za znacznie bardziej futurystyczny. Można się spodziewać, że skóra Lamborghini była szyta ręcznie. Ale te aerodynamicznie wyglądające skrzydła i szpice, wielka karbonowa wanna w sercu Aventadora? To wszystko wygląda jak inżynieria odwrotna z przechwyconego pozaziemskiego lądownika, a nie ręczna robota Włoszki o imieniu Piera. A jednak, jest to wciąż najbardziej ekonomiczny sposób produkcji włókna węglowego. W każdym razie na małą skalę.
„Jeśli mam do wykonania dziesięć części, ręczna robota jest nadal najlepszym sposobem”, mówi Luciano De Oto, szef Centrum Zaawansowanych Badań Kompozytów Lamborghini. „Powyżej 2000 części muszę zwiększyć automatyzację i stosować cięte włókna”. Byłoby to „kute” włókno węglowe, ale do tego jeszcze dojdziemy. Najpierw muszę zapakować próżniowo moją część.
Aby upewnić się, że pierwsza warstwa włókna węglowego jest zgodna z formą, zamykam arkusz w plastiku i wysysam wszelkie kieszenie powietrzne pomiędzy warstwami. Następnie przykrywam to cięższą tkaniną, po czym umieszczam całość w kolejnym grubszym plastikowym worku próżniowym, takim, jakiego używasz do kurczenia kołdry na lato. Po usunięciu uwięzionego powietrza, zakładamy kolejne cztery warstwy, a następnie jeszcze jedną rutynę próżniową po ostatniej warstwie. Jest to żmudne. Firmy takie jak BMW budują zrobotyzowane linie produkcyjne, aby robić to szybciej niż ludzie. Ale nawet wtedy jest to powolne.
Pomijając czasochłonność, proces produkcji włókna węglowego jest również energochłonny. Zamrażarki i okazjonalny wybuch suszarki do włosów to drobiazgi w porównaniu z autoklawem, piecem pod ciśnieniem używanym do utwardzania gotowych części. Mój konkretny kawałek ręcznie układanej dobroci będzie się piekł w piecu przez sześć godzin w temperaturze prawie 400 stopni, a wszystko to pod sześciokrotnie wyższym ciśnieniem niż normalne ciśnienie atmosferyczne. Przynajmniej Lamborghini ma 1,2-megawatowy fotoelektryczny układ słoneczny na dachu fabryki.
Rozwiązanie dla produkcji masowej
Podczas gdy mój komponent się wycisza, udaję się do obszaru, gdzie Lamborghini produkuje części kute. Zamiast starannie utkanego pre-pregu, z którym pracowałem wcześniej, maszyny tutaj używają szorstkiego włókna węglowego znanego jako siekana mata. Kwadraty tego materiału są prasowane w podstawowe kształty nad formą, a następnie przenoszone do ośmiotłokowej kuźni, która wytwarza ciepło o temperaturze 300 stopni i ciśnienie 2900 psi. W przeciwieństwie do pre-pregów, matę ciętą można rozbić na egzotyczne kształty – kotwy śrubowe, cienkie grzbiety – które nie są możliwe do uzyskania podczas ręcznego owijania tkaniny. Proces jest w większości zautomatyzowany i za 20 minut będziemy mieli tę samą część, która potrzebuje jeszcze około pięciu godzin w autoklawie.
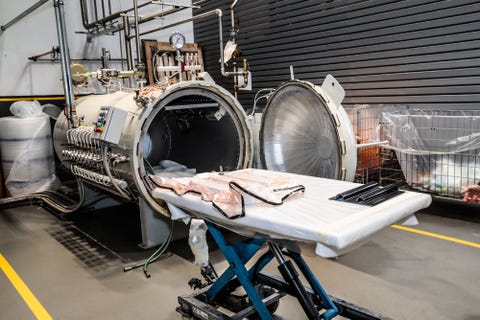
Kuty produkt nie jest tak lekki ani mocny jak rzeczy układane ręcznie, ale jeśli włókno węglowe ma kiedykolwiek przejść do głównego nurtu, to wygląda na to, że jest to właściwa droga. „Diamenty są droższe niż złoto” – mówi De Oto. „Ręcznie układane włókno węglowe nie osiągnie kosztu aluminium, ale w ciągu najbliższych dziesięciu lat, siekana mata może”. Nawet jeśli samochody będą miały tylko cięte maty z włókna węglowego, jak w BMW i3, to i tak będzie to ogromna poprawa w stosunku do aluminium. Lżejsze, więcej mpg, i nie stracił bezpieczeństwa.
Ale wyrafinowane ręcznie układane rzeczy, z jego zamrażarki i autoklawy, worki próżniowe i ściskacze i kruche formy? To zawsze będzie egzotyczny materiał dla egzotycznych samochodów. Lamborghini potrzebuje trzech tygodni na wyprodukowanie każdego Aventadora body-in-white. W fabryce Accorda w Ohio takie tempo nigdy nie przejdzie.
Do godziny 17:00 fabryka się opróżnia, a ja dołączam do pracowników w czarnych fartuchach laboratoryjnych przepływających przez bramę. Nigdy nie widzę części, którą zrobiłem. Nadal jest w autoklawie, a ja nie mam czasu czekać.
Fakty o włóknach węglowych
Thomas Edison stworzył włókna węglowe z bambusa i bawełny, używając ich jako żarników w żarówkach.
Boeing może naprawić drobne uszkodzenia kompozytów węglowych w 787 na bramce, w czasie krótszym niż godzina.
Około 70 procent włókien węglowych jest produkowanych przez Japonię.
Najgłupsza rzecz wykonana z włókna węglowego: fedora z włókna węglowego.
Latający Lekarze
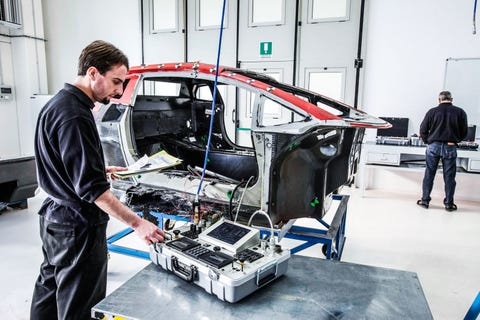
Gdy Aventador ulega awarii, Lamborghini wysyła Latających Lekarzy, techników wyszkolonych do naprawy części z włókna węglowego. Zespół utrzymuje sześć ponadwymiarowych kufrów parowych ze sprzętem do ultradźwięków i przenośnymi maszynami do utwardzania, rozmieszczonych strategicznie na całym świecie. Dlaczego nie nadać ich razem z bagażem? „Celnicy nie lubią mieć do czynienia z chemikaliami” – mówi Casper Steenbergen, szef działu napraw materiałów z włókna węglowego. Poza tym, nie ma potrzeby dodatkowych opóźnień. „Musieliśmy wykonać nowe przyrządy dla całej sekcji panelu wahacza dla samochodu w Chinach”, mówi. „Ta naprawa trwała dwa tygodnie”. Technicy wycinają uszkodzoną sekcję i odbudowują, warstwa po warstwie, aż włókno węglowe uzyska certyfikat zgodności z oryginalną specyfikacją. W rzeczywistości Lamborghini napisało normę ISO 17065, co oznacza, że Ferrari musi przestrzegać zasad Lamborghini, aby certyfikować naprawę zepsutego Enzo. I tak, Latający Lekarze wydają się mieć z tego niezły ubaw.
Ta historia pojawia się w marcu 2017 Popular Mechanics.
.