De ce fibra de carbon este materialul miraculos
Mai rezistentă decât oțelul și cu o fracțiune din greutate, fibra de carbon este o invenție genială. A fost timp de zeci de ani. Junior Johnson construia mașini de curse Nascar care încălcau regulile din acest material în anii ’80. Dar chiar și cu tot acest timp pentru a găsi noi metode de aprovizionare și de producție, fibra de carbon pur și simplu nu încetează să fie scumpă. Cea mai ieftină mașină nouă cu o carcasă din fibră de carbon, Alfa Romeo 4C, are dimensiuni pentru Stuart Little, dar costă la fel de mult ca un Mercedes E-Class. Iar adevăratele trăsuri ale zeilor carbonului, McLarens, Koenigseggs și Lamborghini Aventador ale lumii, sunt propuneri cu șase cifre. Încă nu am reușit să producem acest material în masă la un preț apropiat de cel al aluminiului, ca să nu mai vorbim de cel al oțelului. De ce nu și-a dat nimeni seama cum să facă aceste lucruri să coste mai puțin?
Această întrebare este motivul pentru care mă aflu aici, în Sant’Agata Bolognese, Italia, la instalația de fibră de carbon a Lamborghini, storcând laborios bulele de aer dintr-o foaie de fibră de carbon. Vreau să-i întreb pe băieții în halate de laborator (negre) care produc acest material: De ce nu ne plimbăm în Hyundais cu monococă de carbon?
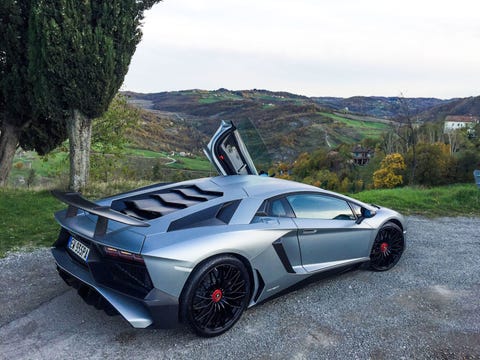
Carbon vs. Oțel
În 2017, pentru a crea componentele metalice care stau la baza majorității mașinilor, se toarnă aluminiul sau oțelul sau magneziul lichid super-încălzit într-o matriță și se toarnă. Îl poți sparge în formă, îl poți sculpta cu o mașină CNC, poți suda piesele împreună. Aveți opțiuni, toate destul de rapide și accesibile. Pentru a face o piesă din fibră de carbon . . . . ei bine, mai întâi scoateți materia primă din congelator.
Rolurile țesute lucioase de fibră de carbon, umplute cu rășină (numită pre-preg) și susținute cu adeziv, sunt depozitate la zero grade Fahrenheit. Dacă este mai cald, rășina se va întări. Această sensibilitate la temperatură înseamnă, de asemenea, că nu puteți tăia materialul în formă cu un laser CNC – pentru a-l păstra rece și maleabil, trebuie să folosiți o lamă, care în cele din urmă se uzează. Chiar și atunci, timpul trece. Din momentul în care se taie prima împletitură a acestor fire de carbon din plastic, aveți la dispoziție aproximativ o zi pentru a-i da formă.
Așa că te grăbești cu spatulele de plastic și forțezi foile negre și argintii într-o matriță, care va fi bună doar pentru aproximativ 300 de utilizări înainte să se deformeze și să fie aruncată la gunoi. Piera, femeia însărcinată să-mi explice toate acestea, pare nedumerită de ritmul meu greoi. Ea scoate un uscător de păr și încălzește materialul pentru a-l face mai maleabil. Dar, bineînțeles, nu vrei prea multă căldură, ca nu cumva materialul preimpregnat să nu se calcifieze prematur în forma greșită.
Futurist, dar lucrat manual
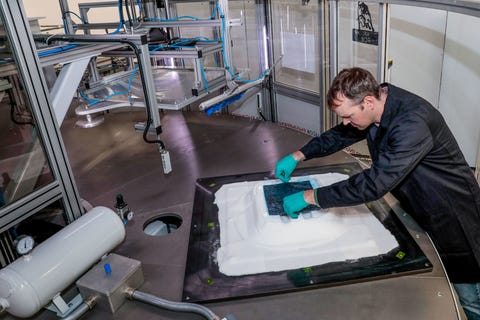
Cu aproximativ un deceniu în urmă, am vizitat o altă fabrică Lamborghini. Am privit o femeie care cosea cu dragoste scaunele unui Murciélago, practicând o marcă de măiestrie metodică care ar fi fost prea laborioasă, prea ineficientă pentru o mașină de masă. Acum, iată-mă din nou aici, asistând la un grad similar de măiestrie manuală investită în crearea unui material pe care noi îl considerăm mult mai futurist. Adică, te-ai aștepta ca pielea Lamborghini să fie cusută manual. Dar acele aripioare și spițe cu aspect aerospațial, tubul mare de carbon din inima lui Aventador? Toate acestea arată ca și cum ar fi fost realizate prin inginerie inversă de la o navă de aterizare extraterestră capturată, nu făcute manual de o italiancă pe nume Piera. Și totuși, acesta este încă cel mai economic mod de a produce fibră de carbon. La scară mică, în orice caz.
„Dacă trebuie să fac zece piese, cel mai bun mod rămâne cel manual”, spune Luciano De Oto, șeful Centrului de cercetare avansată a compozitelor de la Lamborghini. „Peste 2.000 de piese, trebuie să măresc gradul de automatizare și să folosesc fibre tăiate.” Aceasta ar fi fibra de carbon „forjată”, dar vom ajunge și la asta. Mai întâi, trebuie să ambalez piesa în vid.
Pentru a mă asigura că primul strat de fibră de carbon se conformează cu matrița, sigilez foaia în plastic și aspir toate pungile de aer dintre straturi. Apoi, acopăr asta cu o pânză mai grea înainte de a plasa totul într-o altă pungă de plastic mai groasă pentru vid, de genul celei pe care o folosești pentru a-ți micșora plapuma pentru depozitarea pe timp de vară. După ce eliminăm aerul reținut, mai punem încă patru straturi, apoi încă o rutină de vidare după ultimul strat. Este plictisitor. Companii precum BMW construiesc linii de producție robotizate pentru a face acest lucru mai repede decât oamenii. Dar chiar și așa, este lent.
Pe lângă faptul că necesită mult timp, procesul de fabricare a fibrei de carbon este, de asemenea, un consumator de energie. Congelatoarele de depozitare și explozia ocazională cu uscătorul de păr sunt minore în comparație cu autoclava, un cuptor presurizat folosit pentru a polimeriza piesele finite. Bucățica mea specială de bunătate așezată manual se va coace în cuptor timp de șase ore la aproape 400 de grade, totul în timp ce se află sub o presiune de șase ori mai mare decât presiunea atmosferică normală. Cel puțin Lamborghini are un panou solar fotoelectric de 1,2 megawați pe acoperișul fabricii.
O soluție de producție în masă
În timp ce componenta mea se curăță, mă îndrept spre zona în care Lamborghini face piese forjate. În loc de pre-preg-ul bine țesut cu care am lucrat mai devreme, mașinile de aici folosesc o fibră de carbon aspră, cunoscută sub numele de chopped mat. Un pătrat din acest material este presat în forme de bază peste o matriță, apoi este mutat în forja cu opt pistoane, care aplică o căldură de 300 de grade și o presiune de 2.900 psi. Spre deosebire de pre-preg, chopped mat poate fi zdrobit în forme exotice – ancore de șuruburi, creste subțiri – care nu sunt posibile atunci când înfășurați manual țesătura. Procesul este în mare parte automatizat, iar în 20 de minute vom avea aceeași piesă care mai are nevoie de încă aproximativ cinci ore în autoclavă.
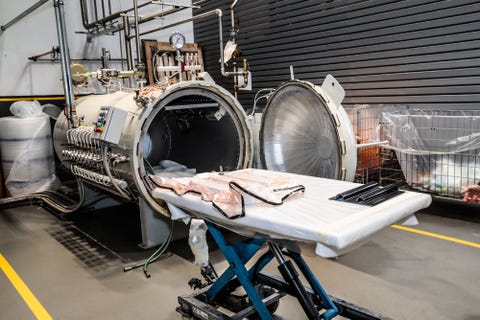
Un produs forjat nu este la fel de ușor sau de puternic ca cel întins de mână, dar dacă fibra de carbon va deveni vreodată mainstream, aceasta pare a fi calea cea mai bună. „Diamantele au un cost mai mare decât aurul”, spune De Oto. „Fibra de carbon așezată manual nu va ajunge la costul aluminiului, dar în următorii zece ani, covorul tocat ar putea ajunge.” Chiar dacă mașinile vor primi doar fibră de carbon cu covor, ca la BMW i3, tot va fi un upgrade uriaș față de aluminiu. Mai ușor, mai mult mpg și nu se pierde siguranța.
Dar chestiile sofisticate așezate manual, cu congelatoarele și autoclavele lor, pungile de vid și racletele și matrițele fragile? Acesta va fi întotdeauna un material exotic pentru mașini exotice. Lamborghini are nevoie de trei săptămâni pentru a produce fiecare caroserie Aventador în alb. Acest ritm nu va merge niciodată la uzina Accord din Ohio.
Până la ora 17:00, fabrica se eliberează, iar eu mă alătur muncitorilor în halate negre de laborator care curg pe poartă. Nu apuc să văd niciodată piesa pe care am făcut-o. Este încă în autoclavă, iar eu nu am timp să aștept.
Fapte despre fibrele de carbon
Thomas Edison a făcut fibre de carbon din bambus și bumbac, folosindu-le ca filamente în becuri.
Boeing poate repara la poartă, în mai puțin de o oră, deteriorări minore ale compozitelor de carbon ale avionului 787.
Aproximativ 70 la sută din fibra de carbon este produsă de Japonia.
Cel mai prostesc lucru făcut din fibră de carbon: fedora din fibră de carbon.
Doctorii Zburători
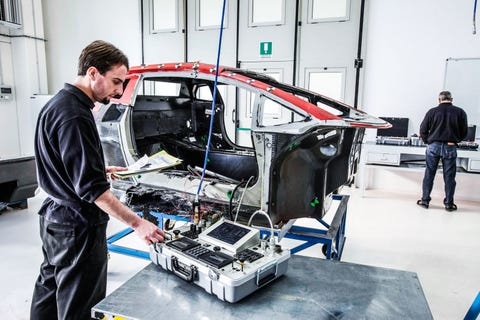
Când un Aventador se prăbușește, Lamborghini îi trimite pe Doctorii Zburători, tehnicieni pregătiți să repare piesele din fibră de carbon. Echipa păstrează șase geamantane cu aburi supradimensionate cu echipamente cu ultrasunete și mașini portabile de vulcanizare poziționate strategic în întreaga lume. De ce să nu le verifice împreună cu bagajele? „Vămilor nu le place să aibă de-a face cu substanțe chimice”, spune Casper Steenbergen, șeful departamentului de reparare a materialelor din fibră de carbon. În plus, nu este nevoie de întârzieri suplimentare. „A trebuit să confecționăm noi șabloane pentru o întreagă secțiune de panou basculant pentru o mașină din China”, spune el. „Această reparație a durat două săptămâni”. Tehnicienii extirpă secțiunea deteriorată și reconstruiesc, strat cu strat, până când fibra de carbon este certificată conform specificațiilor originale. De fapt, Lamborghini a scris standardul, ISO 17065, ceea ce înseamnă că Ferrari trebuie să urmeze regulile Lamborghini pentru a certifica repararea unui Enzo stricat. Și da, Doctorii Zburători par să se bucure de acest lucru.
Acest articol apare în revista Popular Mechanics din martie 2017.
.