Por qué la fibra de carbono es el material milagroso
Más fuerte que el acero y una fracción del peso, la fibra de carbono es un invento brillante. Lo ha sido durante décadas. Junior Johnson estaba construyendo carreras de Nascar con este material en los años 80. Pero a pesar de todo el tiempo que se ha invertido en nuevos métodos de abastecimiento y producción, la fibra de carbono no deja de ser cara. El coche nuevo más barato con carrocería de fibra de carbono, el Alfa Romeo 4C, tiene el tamaño de Stuart Little, pero cuesta tanto como un Mercedes Clase E. Y los verdaderos carros de los dioses del carbono, los McLarens, Koenigseggs y Lamborghini Aventadors del mundo, son propuestas de seis cifras. Todavía no hemos conseguido producirlo en masa a un precio que se acerque al del aluminio, por no hablar del acero. ¿Por qué nadie ha descubierto cómo hacer que estas cosas cuesten menos?
Esa es la razón por la que estoy aquí en Sant’Agata Bolognese, Italia, en las instalaciones de fibra de carbono de Lamborghini, limpiando laboriosamente las burbujas de aire de una hoja de tejido de carbono. Me gustaría preguntar a los tipos con batas (negras) de laboratorio que fabrican este material: ¿Por qué no estamos rodando en Hyundai con monocasco de carbono?
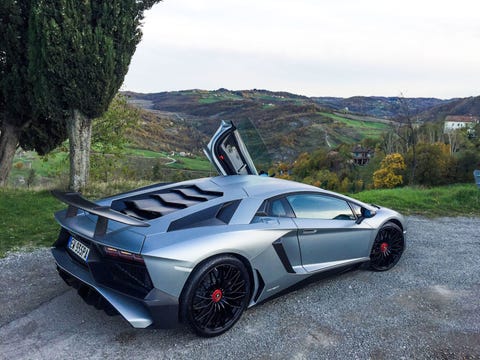
Carbono vs. Acero
En 2017, para crear los componentes metálicos en el núcleo de la mayoría de los coches, se vierte el aluminio líquido súper caliente o el acero o el magnesio en un molde, y se funde. Puedes aplastarlo para darle forma, puedes tallarlo con una máquina CNC, puedes soldar las piezas. Tienes opciones, todas ellas razonablemente rápidas y asequibles. Para hacer una pieza de fibra de carbono… bueno, primero sacas la materia prima del congelador.
Los brillantes rollos de fibra de carbono, rellenos de resina (llamados preimpregnados) y recubiertos de adhesivo, se almacenan a cero grados Fahrenheit. A más temperatura, la resina se endurece. Esta sensibilidad a la temperatura también significa que no se puede cortar el material para darle forma con un láser CNC: para mantenerlo frío y maleable, hay que utilizar una cuchilla, que acaba desgastándose. Incluso entonces, el reloj sigue corriendo. Desde el momento en que se corta la primera trama de estos hilos de plástico de carbono, se tiene aproximadamente un día para darle forma.
Así que te apresuras con las espátulas de plástico y metes a la fuerza las láminas negras y plateadas en un molde, que sólo servirá para unos 300 usos antes de que se deforme y se vaya a la basura. Piera, la mujer encargada de explicarme todo esto, parece desconcertada por mi ritmo lento. Saca un secador de pelo y calienta el material para hacerlo más flexible. Pero, por supuesto, no hay que calentar demasiado, no vaya a ser que el preimpregnado se calcifique prematuramente en la forma equivocada.
Futurista, pero artesanal
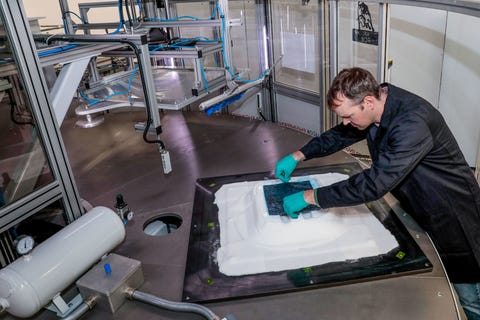
Hace aproximadamente una década, visité otra de las plantas de Lamborghini. Observé a una mujer coser con cariño los asientos de un Murciélago, practicando una marca de artesanía metódica que sería demasiado laboriosa, demasiado ineficiente para un coche del mercado de masas. Ahora, aquí estoy de nuevo, presenciando un grado similar de arte manual invertido en la creación de un material que consideramos mucho más futurista. Es decir, es de esperar que el cuero de Lamborghini haya sido cosido a mano. ¿Pero esas alas y aletas de aspecto aeroespacial, el gran tubo de carbono en el corazón del Aventador? Todo parece haber sido diseñado a partir de una nave de aterrizaje extraterrestre capturada, no hecho a mano por una mujer italiana llamada Piera. Y sin embargo, esta sigue siendo la forma más económica de producir fibra de carbono. A pequeña escala, al menos.
«Si tengo que hacer diez piezas, la fabricación a mano sigue siendo la mejor manera», dice Luciano De Oto, jefe del Centro de Investigación de Composites Avanzados de Lamborghini. «Por encima de 2.000 piezas, necesito aumentar la automatización y utilizar fibra cortada». Eso sería fibra de carbono «forjada», pero ya llegaremos a eso. Primero, tengo que embolsar mi pieza al vacío.
Para asegurar que la primera capa de fibra de carbono se ajuste al molde, sello la hoja en plástico y succiono cualquier bolsa de aire entre las capas. A continuación, lo cubro con una tela más gruesa antes de colocarlo todo dentro de otra bolsa de plástico más gruesa al vacío, del tipo que se utiliza para encoger el edredón para guardarlo en verano. Después de eliminar el aire atrapado, colocamos cuatro capas más, y luego una rutina más de vacío después de la última capa. Es tedioso. Empresas como BMW están construyendo líneas de producción robotizadas para hacer esto más rápido que los humanos. Pero incluso así, es lento.
Además de requerir mucho tiempo, el proceso de fabricación de la fibra de carbono es también un devorador de energía. Los congeladores de almacenamiento y el ocasional chorro de secador de pelo son menores comparados con el autoclave, un horno presurizado utilizado para curar las piezas acabadas. Mi pieza en particular se cuece en el horno durante seis horas a casi 400 grados, a seis veces la presión atmosférica normal. Al menos Lamborghini tiene una matriz solar fotoeléctrica de 1,2 megavatios en el techo de la fábrica.
Una solución de producción en masa
Mientras mi componente se recupera, me dirijo al área donde Lamborghini hace las piezas forjadas. En lugar del preimpregnado pulcramente tejido con el que trabajé antes, las máquinas aquí utilizan una fibra de carbono rugosa conocida como estera picada. Un cuadrado de este material se prensa en formas básicas sobre un molde, y luego se traslada a la forja de ocho pistones, que aplica 300 grados de calor y 2.900 psi de presión. A diferencia del preimpregnado, el material picado puede adoptar formas exóticas -anclajes de tornillo, crestas finas- que no son posibles cuando se envuelve el tejido a mano. El proceso está automatizado en su mayor parte, y en 20 minutos tendremos la misma pieza que aún necesita unas cinco horas más en el autoclave.
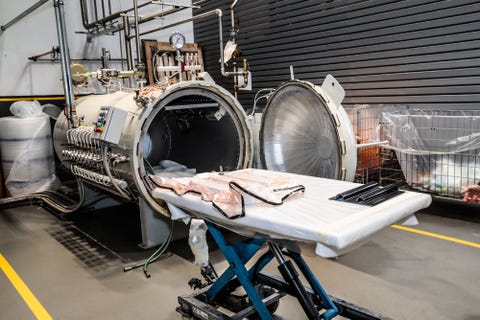
Un producto forjado no es tan ligero ni tan fuerte como el que se coloca a mano, pero si la fibra de carbono va a generalizarse alguna vez, éste parece ser el camino. «Los diamantes son más caros que el oro», dice De Oto. «La fibra de carbono colocada a mano no alcanzará el coste del aluminio, pero en los próximos diez años, la alfombra picada podría hacerlo». Incluso si los coches se limitan a la fibra de carbono cortada, como en el BMW i3, sigue siendo una gran mejora con respecto al aluminio. Más ligero, más mpg, y sin pérdida de seguridad.
¿Pero el sofisticado material manual, con sus congeladores y autoclaves, bolsas de vacío y rasquetas y moldes frágiles? Eso siempre será un material exótico para coches exóticos. Lamborghini necesita tres semanas para producir cada carrocería del Aventador. Ese ritmo nunca va a volar en la planta de Accord en Ohio.
Para las 17:00, la fábrica se está vaciando, y me uno a los trabajadores con batas negras de laboratorio que pasan por la puerta. Nunca veo la pieza que hice. Todavía está en el autoclave, y no tengo tiempo para esperar.
Hechos sobre la fibra de carbono
Thomas Edison hizo fibras de carbono con bambú y algodón, usándolas como filamentos en las bombillas.
Boeing puede reparar pequeños daños en los compuestos de carbono del 787 en la puerta de embarque, en menos de una hora.
Alrededor del 70 por ciento de la fibra de carbono se produce en Japón.
La cosa más tonta hecha de fibra de carbono: el fedora de fibra de carbono.
Los Flying Doctors
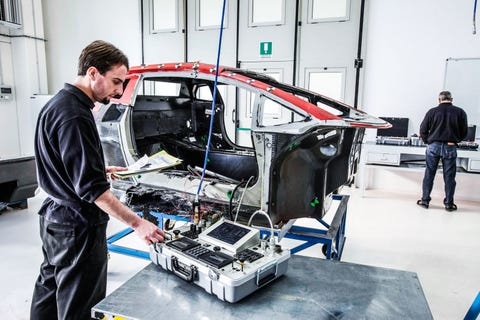
Cuando un Aventador sufre un accidente, Lamborghini envía a los Flying Doctors, técnicos capacitados para reparar piezas de fibra de carbono. El equipo mantiene seis baúles de vapor de gran tamaño con equipos de ultrasonido y máquinas de curado portátiles colocados estratégicamente en todo el mundo. ¿Por qué no lo facturan con su equipaje? «A las aduanas no les gusta tratar con productos químicos», dice Casper Steenbergen, jefe de reparación de materiales de fibra de carbono. Además, no hay necesidad de retrasos adicionales. «Tuvimos que hacer nuevas plantillas para toda una sección del panel de balancines de un coche en China», dice. «Esa reparación nos llevó dos semanas». Los técnicos extirpan la sección dañada y la reconstruyen, capa por capa, hasta que la fibra de carbono está certificada con las especificaciones originales. De hecho, Lamborghini escribió la norma, ISO 17065, lo que significa que Ferrari tiene que seguir las reglas de Lamborghini para certificar la reparación de un Enzo roto. Y sí, parece que a los Flying Doctors les hace gracia.
Esta historia aparece en la revista Popular Mechanics de marzo de 2017.