炭素繊維が奇跡の素材である理由
鉄よりも強く、重さは数分の一という炭素繊維は、素晴らしい発明です。 何十年も前からそうでした。 ジュニア・ジョンソンは、80年代にこの材料で、ルールを破るナスカーレーサーを作りました。 しかし、新しい調達や生産方法を考え出すのに時間がかかっても、カーボンファイバーは高価であることに変わりはありません。 カーボンファイバー製の車体を持つ最も安価な新車、アルファロメオ4Cはスチュアート・リトル並みのサイズでありながら、メルセデスEクラスと同等の価格です。 マクラーレンやケーニッヒゼグ、ランボルギーニ・アヴェンタドールといったカーボンの神様の戦車は、6桁の値段で売られている。 鉄はおろか、アルミに近い価格での大量生産はまだ実現していないのだ。 なぜ誰も、この素材をより安く作る方法を見つけ出さないのでしょうか?
その疑問が、私がここイタリアのサンタガタ・ボロニェーゼにあるランボルギーニのカーボンファイバー工場で、カーボン織物のシートから苦労して気泡をすくい取っている理由です。 この素材を作っている白衣の男たちに聞いてみたい。 なぜ、私たちはカーボン・モノコックのヒュンダイに乗らないのですか?
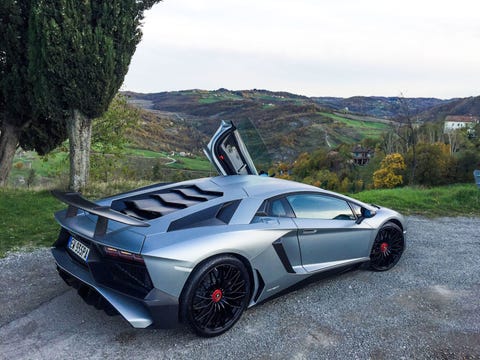
Carbon vs. Steel
2017年、ほとんどの車の核となる金属部品を作るには、超高温の液体アルミニウムかスチールかマグネシウムを型に流し込んで、それを鋳造するのです。 それを粉砕して形にしたり、CNCマシンで彫ったり、部品を溶接したりすることができます。 どれも手頃な価格でスピーディにできる方法です。 カーボンファイバーから部品を作るには、まず冷凍庫から原料を取り出します。
光沢のあるカーボンファイバーの織物ロールは、樹脂(プリプレグと呼ばれる)で満たされ、接着剤で裏打ちされて、華氏0度で保管されています。 これ以上温度が高いと、樹脂が固まってしまうのです。 そのため、CNCレーザーで切断することができず、刃物を使うことになるが、刃物は摩耗してしまう。 それでも、時間はかかる。 このプラスチックカーボンの糸を最初に切ってから、約1日で形を整えることができるのです。
そこで、急いでプラスチックのヘラを使い、黒と銀のシートを型に押し込んでいきますが、型が変形してゴミになるまでには、300回ほどしか使えません。 この説明を担当したピエラは、私のたどたどしいペースに戸惑っているようだ。 ドライヤーで温めて、よりしなやかな素材にするのだ。 もちろん、熱しすぎてプリプレグの形が崩れてしまうのは困りものですが。
未来的だが手作り
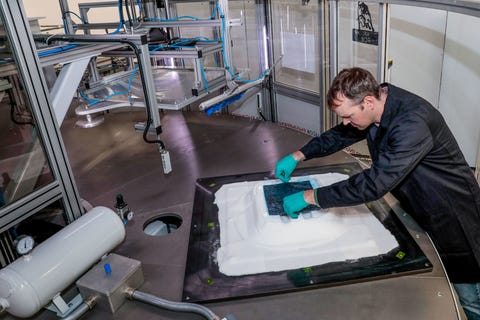
最初のカーボンファイバーの層が金型に適合するように、シートをプラスチックで密閉し、層間のエアポケットを吸い取ります。 さらにその上から厚手の布で覆って、夏場に布団を縮めるときに使うような厚手の真空ビニール袋に全体を入れるんです。 空気を抜いた後、さらに4層重ね、最終層の後にもう1回掃除機をかけます。 面倒ですね。 BMWのような企業は、人間よりも速くこれを行うために、ロボットの生産ラインを構築しています。 でも、それでも遅いんです。
時間がかかるだけでなく、炭素繊維の製造工程はエネルギーを大量に消費します。 冷凍庫やドライヤーの使用は、オートクレーブ(完成した部品を硬化させるための加圧炉)に比べれば些細なことです。 私の手織り製品は、通常の6倍の気圧の下、400度近い温度で6時間かけて焼かれるのです。 少なくともランボルギーニは、工場の屋根に1.2メガワットの光電式太陽電池アレイを備えている。
大量生産ソリューション
部品が硬化する間、ランボルギーニが鍛造部品を作っているエリアに向かいました。 先ほどのきれいに編まれたプリプレグの代わりに、ここの機械ではチョップドマットと呼ばれる粗いカーボンファイバーが使われています。 この四角い素材を金型の上で基本形にプレスし、300度の熱と2,900psiの圧力をかける8ピストン鍛造機に移動させるのです。 プリプレグとは異なり、チョップドマットは、手で布を包むときには不可能なスクリューアンカーや薄いリッジなど、エキゾチックな形状に打ち抜くことができるのです。 工程はほとんど自動化されており、20分後にはオートクレーブであと5時間くらいかかるのと同じ部品ができあがります。
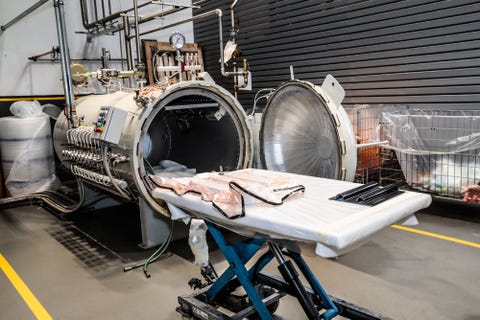
鍛造製品は、手で巻いたものほど軽くも強くもありませんが、炭素繊維が主流となるならば、これは方法のように見えますね。 「ダイヤモンドは金よりもコストが高い」とデ・オトは言う。 「しかし、今後10年以内に、チョップドマットはアルミニウムのコストに追いつくかもしれません」。 BMW i3のように、チョップド・マット・カーボンファイバーが採用されただけでも、アルミニウムから大きくアップグレードされたことには変わりありません。 より軽く、より燃費がよく、安全性も損なわれない。
しかし、冷凍庫やオートクレーブ、真空バッグ、スキージ、壊れやすい金型など、手作業で作られた精巧なものはどうでしょうか。 それは常にエキゾチックな車のためのエキゾチックな材料であるでしょう。 ランボルギーニは、アヴェンタドールのボディ・イン・ホワイトを1台生産するのに3週間を要します。 オハイオ州のアコード工場では、このペースは絶対に無理だ。
17:00には工場は撤収し、私は黒い白衣を着た労働者たちと一緒に門をくぐった。 私は自分が作った部品を見ることはありませんでした。
炭素繊維の事実
トーマス・エジソンは竹と綿から炭素繊維を作り、電球のフィラメントとして使用しました。
ボーイングは、787のカーボン複合材の小さな損傷をゲートで1時間以内に修理することができます。
炭素繊維の約70%は日本が生産しています。
炭素繊維で作られた最も間抜けなもの:炭素繊維のフェドーラ。
フライングドクター
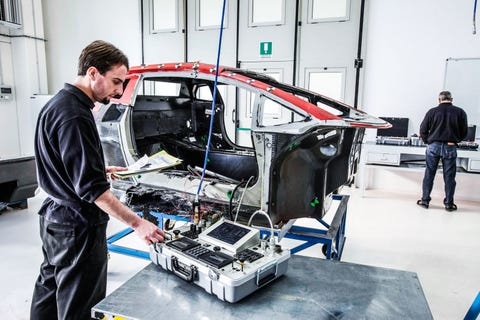
アヴェンタドールがクラッシュすると、ランボルギーニはカーボンファイバーの部品を修理するために訓練を受けた技術者、フライングドクターを送り込みました。 このチームは、超音波診断装置とポータブル硬化機を入れた6つの特大スチーマー・トランクを、世界中に戦略的に配置しています。 なぜ、手荷物と一緒に預けないのか? 「税関は化学物質を扱うのを嫌いますから」と、炭素繊維材料修理担当のキャスパー・スティーンベルゲン(Casper Steenbergen)は言う。 それに、追加の遅延も必要ない。 「中国のあるクルマでは、ロッカーパネル全体の治具を新しく作り直さなければなりませんでした。 「その修理には2週間かかりました」。 技術者は損傷した部分を切除し、カーボンファイバーが元の仕様に適合することが証明されるまで、一層ずつ作り直していきます。 実際、ランボルギーニがISO17065という規格を作ったので、フェラーリは壊れたエンツォの修理を証明するためにランボルギーニのルールに従わなければならないのである。 そうそう、フライング・ドクターはそのことに興奮するみたいですよ。
この記事は2017年3月のPopular Mechanicsに掲載されています
で詳細を確認することができます。