Warum Kohlefaser das Wundermaterial ist
Stärker als Stahl und ein Bruchteil des Gewichts, ist Kohlefaser eine geniale Erfindung. Und das schon seit Jahrzehnten. Junior Johnson baute in den 80er Jahren Nascar-Rennwagen aus dem Material, die alle Regeln brachen. Aber trotz all der Zeit, die für die Entwicklung neuer Beschaffungs- und Produktionsmethoden zur Verfügung stand, wird Kohlefaser immer noch teuer sein. Der billigste Neuwagen mit einer Karbonfaserwanne, der Alfa Romeo 4C, hat die Größe eines Stuart Little, kostet aber so viel wie eine Mercedes E-Klasse. Und die wirklichen Wagen der Karbon-Götter, die McLarens und Königseggs und Lamborghini Aventadors dieser Welt, sind ausschließlich sechsstellige Angebote. Wir haben es immer noch nicht geschafft, das Material in Massenproduktion zu einem Preis herzustellen, der auch nur annähernd dem von Aluminium oder gar Stahl entspricht. Warum hat noch niemand herausgefunden, wie man das Zeug billiger machen kann?
Diese Frage ist der Grund, warum ich hier in Sant’Agata Bolognese, Italien, in Lamborghinis Karbonfaserwerk bin und mühsam Luftblasen aus einer Karbonfaserplatte herausquetsche. Ich möchte die Jungs in (schwarzen) Laborkitteln fragen, die dieses Material herstellen: Warum fahren wir nicht in Hyundais mit Carbon-Monocoque herum?
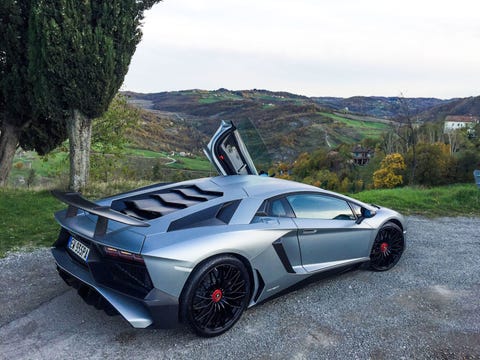
Carbon vs. Stahl
Im Jahr 2017 gießt man für die Metallkomponenten, die den Kern der meisten Autos bilden, superheißes flüssiges Aluminium oder Stahl oder Magnesium in eine Form und gießt es. Man kann es in Form schlagen, man kann es mit einer CNC-Maschine schnitzen, man kann Teile zusammenschweißen. Es gibt verschiedene Möglichkeiten, die alle relativ schnell und kostengünstig sind. Um ein Teil aus Kohlefaser herzustellen … nun, zuerst holt man das Rohmaterial aus der Tiefkühltruhe.
Die glänzenden, gewebten Rollen aus Kohlefaser, die mit Harz gefüllt (Pre-Preg genannt) und mit Klebstoff versehen sind, werden bei null Grad gelagert. Je wärmer es ist, desto mehr härtet das Harz aus. Diese Temperaturempfindlichkeit bedeutet auch, dass man das Material nicht mit einem CNC-Laser in Form schneiden kann – um es kühl und formbar zu halten, muss man eine Klinge verwenden, die sich irgendwann abnutzt. Und selbst dann tickt die Uhr. Ab dem Zeitpunkt, an dem das erste Geflecht dieser Kunststoff-Kohlefäden geschnitten wird, hat man etwa einen Tag Zeit, um es in Form zu bringen.
Also beeilt man sich mit den Plastikspateln und presst die schwarzen und silbernen Platten in eine Form, die nur etwa 300 Mal benutzt werden kann, bevor sie sich verformt und entsorgt wird. Piera, die Frau, die mir das alles erklären soll, scheint über meine Schwerfälligkeit verwirrt zu sein. Sie holt einen Fön hervor und erwärmt das Material, um es geschmeidiger zu machen. Aber man will natürlich nicht zu viel Hitze, damit das Prepreg nicht vorzeitig in der falschen Form verkalkt.
Futuristisch, aber handgefertigt
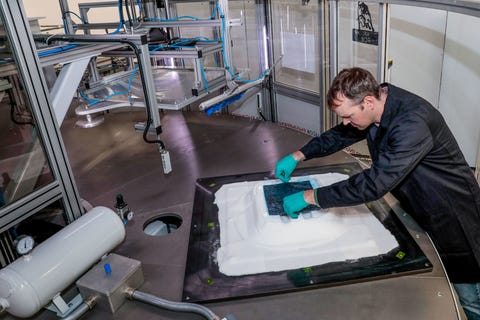
Vor etwa einem Jahrzehnt besuchte ich ein anderes Werk von Lamborghini. Ich beobachtete eine Frau, die liebevoll die Sitze eines Murciélago nähte und dabei eine methodische Handwerkskunst praktizierte, die für ein Massenauto zu mühsam, zu ineffizient wäre. Jetzt bin ich wieder hier und erlebe ein ähnliches Maß an handwerklicher Kunstfertigkeit bei der Herstellung eines Materials, das wir für viel futuristischer halten. Ich meine, man kann davon ausgehen, dass das Leder von Lamborghini von Hand genäht wurde. Aber die aus der Luft stammenden Kotflügel und Sporen, die große Karbonwanne im Herzen des Aventador? All das sieht aus, als wäre es aus einem erbeuteten außerirdischen Landegerät nachgebaut und nicht von einer Italienerin namens Piera handgefertigt worden. Und doch ist dies immer noch die wirtschaftlichste Art, Kohlefaser zu produzieren. Zumindest in kleinem Maßstab.
„Wenn ich zehn Teile herstellen muss, ist Handarbeit immer noch die beste Methode“, sagt Luciano De Oto, Leiter des Advanced Composite Research Center von Lamborghini. „Bei mehr als 2.000 Teilen muss ich die Automatisierung erhöhen und gehackte Fasern verwenden. Das wäre „geschmiedete“ Kohlefaser, aber dazu kommen wir gleich noch. Zuerst muss ich mein Teil vakuumverpacken.
Um sicherzustellen, dass sich die erste Lage Kohlefaser an die Form anpasst, versiegele ich die Platte in Plastik und sauge alle Lufteinschlüsse zwischen den Lagen heraus. Dann decke ich sie mit einem schwereren Stoff ab, bevor ich das Ganze in einen weiteren, dickeren Plastikvakuumbeutel lege, wie man ihn zum Einschweißen einer Bettdecke für den Sommer verwendet. Nachdem ich die eingeschlossene Luft entfernt habe, lege ich vier weitere Lagen ein, und nach der letzten Lage folgt eine weitere Vakuumroutine. Das ist mühsam. Unternehmen wie BMW bauen Roboteranlagen, die diese Arbeit schneller erledigen als Menschen. Aber selbst dann ist es langsam.
Die Herstellung von Karbonfasern ist nicht nur zeitintensiv, sondern auch ein Energiefresser. Die Gefrierschränke und der gelegentliche Föhn sind unbedeutend im Vergleich zum Autoklaven, einem Druckofen, der zum Aushärten der fertigen Teile verwendet wird. Mein spezielles Stück handgelegter Güte wird in diesem Ofen sechs Stunden lang bei fast 400 Grad gebacken, und das alles unter dem Sechsfachen des normalen atmosphärischen Drucks. Wenigstens hat Lamborghini eine 1,2-Megawatt-Solaranlage auf dem Dach des Werks.
Eine Lösung für die Massenproduktion
Während mein Bauteil kuriert wird, gehe ich zu dem Bereich, in dem Lamborghini Schmiedeteile herstellt. Anstelle des sauber gewebten Pre-Pregs, mit dem ich zuvor gearbeitet habe, verwenden die Maschinen hier eine grobe Kohlefaser, die als Chopped Mat bekannt ist. Ein Quadrat dieses Materials wird über einer Form in Grundformen gepresst und dann in die Acht-Kolben-Schmiede gebracht, die mit 300 Grad Hitze und einem Druck von 2.900 psi arbeitet. Im Gegensatz zu Prepreg kann Schnittmatte in exotische Formen gepresst werden – Schraubanker, dünne Rippen -, die beim manuellen Einwickeln von Gewebe nicht möglich sind. Der Prozess ist größtenteils automatisiert, und in 20 Minuten haben wir das gleiche Teil, das noch etwa fünf Stunden im Autoklaven braucht.
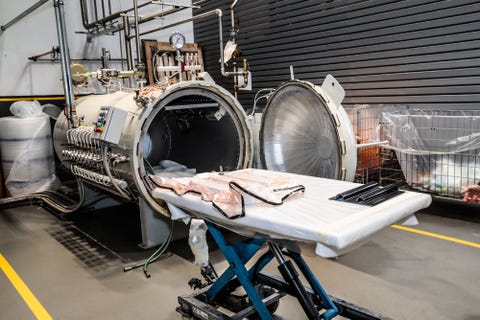
Ein geschmiedetes Produkt ist nicht so leicht oder stark wie das von Hand gelegte Zeug, aber wenn Kohlefaser jemals Mainstream werden soll, sieht dies wie der Weg aus. „Diamanten sind teurer als Gold“, sagt De Oto. „Handgelegte Karbonfasern werden nicht die Kosten von Aluminium erreichen, aber in den nächsten zehn Jahren könnte dies bei geschnittener Matte der Fall sein. Selbst wenn die Autos nur mit Kohlefaser in Form von Schnittmatten ausgestattet sind, wie beim BMW i3, ist das immer noch eine enorme Verbesserung gegenüber Aluminium. Leichter, mehr Treibstoffverbrauch und kein Verlust an Sicherheit.
Aber das hochentwickelte handgelegte Material, mit seinen Gefrierschränken und Autoklaven, Vakuumbeuteln und Rakeln und zerbrechlichen Formen? Das wird immer ein exotisches Material für exotische Autos sein. Lamborghini braucht drei Wochen, um jede Aventador-Rohkarosserie herzustellen. So schnell wird es im Accord-Werk in Ohio nie gehen.
Um 17:00 Uhr wird das Werk geräumt, und ich schließe mich den Arbeitern in schwarzen Laborkitteln an, die durch das Tor strömen. Das Teil, das ich hergestellt habe, sehe ich nie. Es ist immer noch im Autoklaven, und ich habe keine Zeit zu warten.
Fakten zu Kohlenstofffasern
Thomas Edison stellte Kohlenstofffasern aus Bambus und Baumwolle her und verwendete sie als Glühfäden in Glühbirnen.
Boeing kann kleinere Schäden an den Kohlefaserverbundwerkstoffen der 787 am Flugsteig in weniger als einer Stunde reparieren.
Ungefähr 70 Prozent der Kohlefasern werden in Japan hergestellt.
Das Dümmste, was aus Kohlefaser hergestellt wurde: der Kohlefaser-Fedora.
Die Flying Doctors
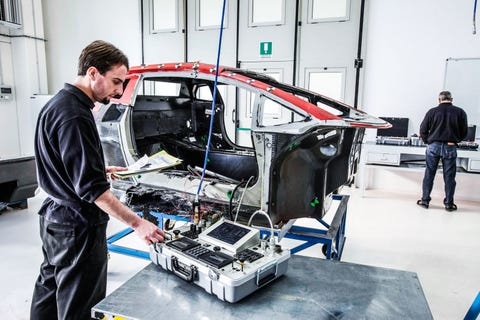
Wenn ein Aventador verunglückt, schickt Lamborghini die Flying Doctors los, Techniker, die für die Reparatur von Kohlefaserteilen ausgebildet sind. Das Team verfügt über sechs überdimensionale Dampfkoffer mit Ultraschallgeräten und tragbaren Aushärtungsmaschinen, die strategisch um die Welt verteilt sind. Warum sollte man sie nicht mit dem Gepäck einchecken? „Der Zoll hat nicht gern mit Chemikalien zu tun“, sagt Casper Steenbergen, Leiter der Reparatur von Karbonfasern. Außerdem gibt es keinen Grund für zusätzliche Verzögerungen. „Wir mussten für ein Auto in China neue Vorrichtungen für eine ganze Schwellerpartie anfertigen“, erzählt er. „Diese Reparatur dauerte zwei Wochen.“ Die Techniker schneiden den beschädigten Teil heraus und bauen ihn Schicht für Schicht wieder auf, bis die Kohlefaser den ursprünglichen Spezifikationen entspricht. Tatsächlich hat Lamborghini die Norm ISO 17065 geschrieben, was bedeutet, dass Ferrari die Regeln von Lamborghini befolgen muss, um die Reparatur eines kaputten Enzo zu zertifizieren. Und ja, die Flying Doctors scheinen sich einen Spaß daraus zu machen.
Diese Geschichte erscheint in der März 2017 Popular Mechanics.
.