Perché la fibra di carbonio è il materiale miracoloso
Più forte dell’acciaio e una frazione del peso, la fibra di carbonio è un’invenzione brillante. Lo è stata per decenni. Junior Johnson stava costruendo piloti di Nascar con questa roba negli anni ’80. Ma anche con tutto quel tempo per trovare nuovi metodi di approvvigionamento e produzione, la fibra di carbonio non smette di essere costosa. La nuova auto più economica con una vasca in fibra di carbonio, l’Alfa Romeo 4C, ha le dimensioni di Stuart Little, ma costa quanto una Mercedes Classe E. E i veri carri degli dei del carbonio, le McLaren e le Koenigsegg e le Lamborghini Aventador del mondo, sono proposte rigorosamente a sei cifre. Non siamo ancora riusciti a produrre in massa questa roba a qualcosa che si avvicini al prezzo dell’alluminio, per non parlare dell’acciaio. Perché nessuno ha capito come far costare meno questa roba?
Questa domanda è il motivo per cui sono qui a Sant’Agata Bolognese, in Italia, presso lo stabilimento Lamborghini in fibra di carbonio, a spurgare faticosamente le bolle d’aria da un foglio di tessuto di carbonio. Voglio chiedere ai ragazzi in camice (nero) che producono questo materiale: Perché non stiamo girando in Hyundai con la monoscocca di carbonio?
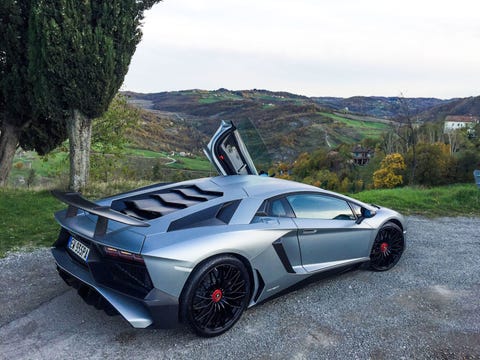
Carbonio contro acciaio
Nel 2017, per creare i componenti metallici alla base della maggior parte delle auto, si versa l’alluminio liquido super-caldo o l’acciaio o il magnesio in uno stampo e lo si fonde. Si può spaccare in forma, si può scolpire con una macchina CNC, si possono saldare i pezzi insieme. Hai delle opzioni, tutte ragionevolmente veloci e convenienti. Per fare un pezzo in fibra di carbonio… beh, prima si tira fuori la materia prima dal congelatore.
I lucidi rotoli di fibra di carbonio, riempiti di resina (chiamata pre-preg) e ricoperti di adesivo, sono conservati a zero gradi Fahrenheit. Se è più caldo, la resina si indurisce. Questa sensibilità alla temperatura significa anche che non si può tagliare il materiale in forma con un laser CNC – per mantenerlo freddo e malleabile, è necessario utilizzare una lama, che alla fine si consuma. Anche allora, il tempo scorre. Dal momento in cui si taglia la prima trama di questi fili di carbonio plastico, si ha circa un giorno per dargli forma.
Così ci si affretta con le spatole di plastica e si forzano i fogli neri e argento in uno stampo, che sarà buono solo per circa 300 usi prima che si deformi e venga cestinato. Piera, la donna incaricata di spiegarmi tutto questo, sembra sconcertata dal mio passo lento. Prende un asciugacapelli e riscalda il materiale per renderlo più flessibile. Ma naturalmente, non si vuole troppo calore, per evitare che il pre-preg si calcifichi prematuramente nella forma sbagliata.
Futuristico ma artigianale
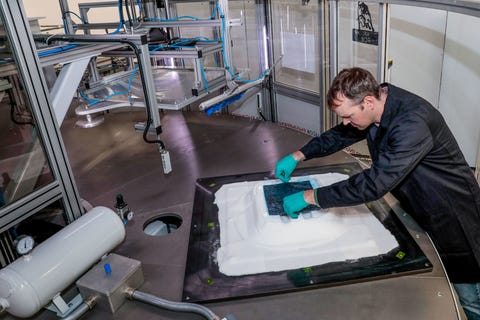
Circa dieci anni fa, ho visitato un altro stabilimento della Lamborghini. Ho visto una donna cucire amorevolmente i sedili di una Murciélago, praticando un tipo di artigianato metodico che sarebbe troppo laborioso, troppo inefficiente per un’auto di massa. Ora, eccomi di nuovo qui, testimone di un simile grado di maestria manuale investito nella creazione di un materiale che pensiamo come molto più futuristico. Insomma, ci si aspetta che la pelle della Lamborghini sia stata cucita a mano. Ma quelle ali dall’aspetto aerospaziale e le ghette, la grande vasca in carbonio nel cuore della Aventador? Sembra che tutto sia stato progettato al contrario da un mezzo di atterraggio extraterrestre catturato, non fatto a mano da una donna italiana di nome Piera. Eppure, questo è ancora il modo più economico per produrre fibra di carbonio. Su piccola scala, comunque.
“Se devo fare dieci pezzi, il fatto a mano è ancora il modo migliore”, dice Luciano De Oto, capo del Centro di Ricerca Avanzata sui Compositi della Lamborghini. “Sopra le 2.000 parti, devo aumentare l’automazione e usare la fibra tagliata”. Questa sarebbe la fibra di carbonio “forgiata”, ma ci arriveremo. Per prima cosa, devo imbustare il mio pezzo sottovuoto.
Per assicurarmi che il primo strato di fibra di carbonio sia conforme allo stampo, sigillo il foglio nella plastica e aspiro qualsiasi sacca d’aria tra gli strati. Poi, lo copro con un panno più pesante prima di mettere il tutto all’interno di un altro sacco di plastica più spesso per il vuoto, del tipo che si usa per restringere il piumone per la conservazione estiva. Dopo aver rimosso l’aria intrappolata, mettiamo altri quattro strati, poi un altro vuoto di routine dopo lo strato finale. È noioso. Aziende come la BMW stanno costruendo linee di produzione robotizzate per farlo più velocemente degli umani. Ma anche così, è lento.
Oltre ad essere dispendioso in termini di tempo, il processo di produzione della fibra di carbonio è anche un ingordo di energia. I congelatori di stoccaggio e le occasionali esplosioni con l’asciugacapelli sono minori rispetto all’autoclave, un forno pressurizzato usato per curare le parti finite. Il mio particolare pezzo di bontà rivestito a mano cuocerà nel forno per sei ore a quasi 400 gradi, il tutto sotto sei volte la normale pressione atmosferica. Almeno la Lamborghini ha un impianto solare fotoelettrico da 1,2 megawatt sul tetto della fabbrica.
Una soluzione per la produzione di massa
Mentre il mio componente è in attesa, mi dirigo verso l’area dove la Lamborghini produce pezzi forgiati. Invece del pre-preg a trama ordinata con cui ho lavorato prima, le macchine qui usano una fibra di carbonio grezza nota come chopped mat. Un quadrato di questo materiale viene pressato in forme di base su uno stampo, poi spostato nella forgia a otto pistoni, che applica 300 gradi di calore e 2.900 psi di pressione. A differenza del pre-preg, il chopped mat può essere schiacciato in forme esotiche – ancoraggi a vite, creste sottili – che non sono possibili quando si avvolge il tessuto a mano. Il processo è per lo più automatizzato, e in 20 minuti avremo la stessa parte che ha ancora bisogno di altre cinque ore in autoclave.
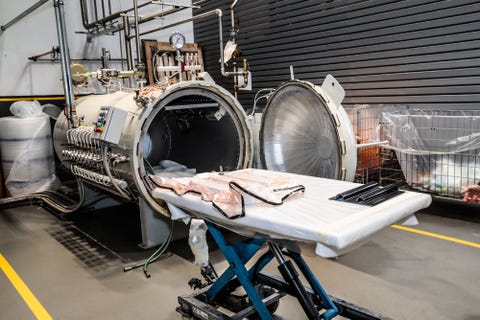
Un prodotto forgiato non è così leggero o forte come quello fatto a mano, ma se la fibra di carbonio diventerà mai mainstream, questo sembra il modo giusto. “I diamanti hanno un costo più alto dell’oro”, dice De Oto. “La fibra di carbonio lavorata a mano non raggiungerà il costo dell’alluminio, ma nei prossimi dieci anni il tappetino tagliato potrebbe farlo”. Anche se le auto hanno solo la fibra di carbonio tagliata, come nella BMW i3, si tratta comunque di un enorme miglioramento rispetto all’alluminio. Più leggero, più mpg, e nessuna sicurezza persa.
Ma la sofisticata roba fatta a mano, con i suoi congelatori e autoclavi, sacchi a vuoto e spatole e stampi fragili? Quello sarà sempre un materiale esotico per auto esotiche. La Lamborghini ha bisogno di tre settimane per produrre ogni carrozzeria Aventador. Quel ritmo non volerà mai nello stabilimento Accord in Ohio.
Per le 17:00, la fabbrica si sta svuotando, e mi unisco agli operai in camice nero che attraversano il cancello. Non vedo mai il pezzo che ho fatto. È ancora nell’autoclave, e non ho tempo di aspettare.
Fatti sulla fibra di carbonio
Thomas Edison ha ricavato le fibre di carbonio da bambù e cotone, usandole come filamenti nelle lampadine.
Boeing può riparare piccoli danni ai compositi di carbonio del 787 al gate, in meno di un’ora.
Circa il 70% della fibra di carbonio è prodotta dal Giappone.
La cosa più stupida fatta in fibra di carbonio: il fedora in fibra di carbonio.
I Flying Doctors
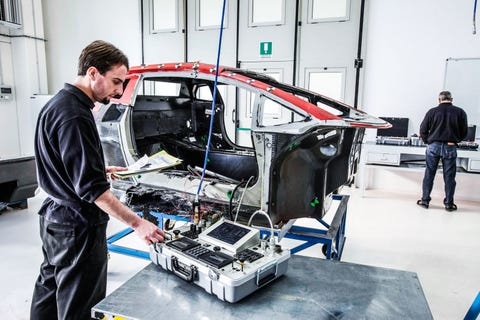
Quando una Aventador si schianta, la Lamborghini manda i Flying Doctors, tecnici addestrati a riparare parti in fibra di carbonio. Il team tiene sei bauli a vapore oversize con attrezzature a ultrasuoni e macchine di polimerizzazione portatili posizionate strategicamente in tutto il mondo. Perché non controllarli insieme ai loro bagagli? “Alla dogana non piace avere a che fare con i prodotti chimici”, dice Casper Steenbergen, responsabile della riparazione dei materiali in fibra di carbonio. Inoltre, non c’è bisogno di ulteriori ritardi. “Abbiamo dovuto fare nuove maschere per un’intera sezione del rocker-panel di un’auto in Cina”, dice. “Quella riparazione ha richiesto due settimane”. I tecnici rimuovono la sezione danneggiata e la ricostruiscono, strato dopo strato, fino a quando la fibra di carbonio è certificata secondo le specifiche originali. Infatti, la Lamborghini ha scritto lo standard, ISO 17065, il che significa che la Ferrari deve seguire le regole della Lamborghini per certificare la riparazione di una Enzo rotta. E sì, i dottori volanti sembrano essere entusiasti di questo.
Questa storia appare nel Popular Mechanics di marzo 2017.