Pourquoi la fibre de carbone est le matériau miracle
Plus solide que l’acier et une fraction du poids, la fibre de carbone est une invention géniale. Elle l’a été pendant des décennies. Junior Johnson construisait des voitures de course Nascar en respectant les règles, dans les années 80. Mais même avec tout ce temps pour trouver de nouvelles méthodes d’approvisionnement et de production, la fibre de carbone ne cesse d’être chère. La nouvelle voiture la moins chère dotée d’une coque en fibre de carbone, l’Alfa Romeo 4C, est de la taille d’une Stuart Little, mais coûte autant qu’une Mercedes Classe E. Et les véritables chars des dieux du carbone, les McLaren, Koenigsegg et Lamborghini Aventadors du monde entier, sont strictement des propositions à six chiffres. Nous n’avons toujours pas réussi à produire ce matériau en masse à un prix proche de celui de l’aluminium, sans parler de l’acier. Pourquoi personne n’a encore trouvé le moyen de faire baisser le prix de ces produits ?
Cette question est la raison pour laquelle je suis ici à Sant’Agata Bolognese, en Italie, dans l’usine de fibre de carbone de Lamborghini, en train d’essuyer laborieusement les bulles d’air d’une feuille de carbone tissé. Je voudrais demander aux gars en blouse (noire) qui fabriquent ce matériau : Pourquoi on ne roule pas dans des Hyundais monocoques en carbone ?
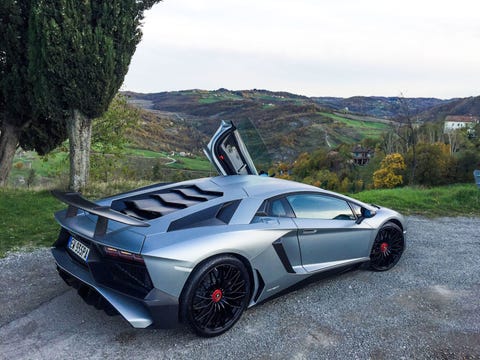
Carbone contre acier
En 2017, pour créer les composants métalliques au cœur de la plupart des voitures, vous versez votre aluminium ou acier ou magnésium liquide super chaud dans un moule, et vous le coulez. Vous pouvez le frapper pour lui donner une forme, vous pouvez le sculpter avec une machine CNC, vous pouvez souder des pièces ensemble. Vous avez plusieurs options, toutes raisonnablement rapides et abordables. Pour fabriquer une pièce en fibre de carbone… il faut d’abord sortir la matière première du congélateur.
Les rouleaux tissés brillants de fibre de carbone, remplis de résine (appelée préimprégnée) et soutenus par un adhésif, sont stockés à zéro degré Fahrenheit. S’il fait plus chaud, la résine durcira. Cette sensibilité à la température signifie également qu’il n’est pas possible de découper le matériau à l’aide d’un laser CNC – pour le garder froid et malléable, il faut utiliser une lame, qui finit par s’user. Même dans ce cas, l’heure tourne. À partir du moment où le premier tissage de ces fils de carbone en plastique est coupé, vous avez environ une journée pour le façonner.
Alors, vous vous hâtez avec les spatules en plastique et forcez les feuilles noires et argentées dans un moule, qui ne sera bon que pour environ 300 utilisations avant d’être déformé et mis à la poubelle. Piera, la femme chargée de m’expliquer tout cela, semble déconcertée par ma lenteur. Elle sort un sèche-cheveux et chauffe le matériau pour le rendre plus souple. Mais bien sûr, vous ne voulez pas trop de chaleur, de peur que votre pré-imprégné ne se calcifie prématurément dans la mauvaise forme.
Futuriste mais artisanal
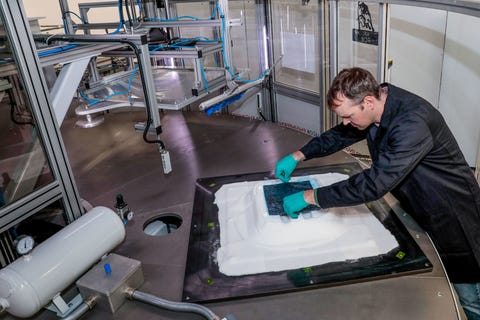
Il y a environ dix ans, j’ai visité une autre usine de Lamborghini. J’ai regardé une femme coudre avec amour les sièges d’une Murciélago, pratiquant une marque d’artisanat méthodique qui serait trop laborieuse, trop inefficace pour une voiture de grande diffusion. Aujourd’hui, je suis à nouveau témoin d’un degré similaire d’art manuel investi dans la création d’un matériau que nous considérons comme beaucoup plus futuriste. Je veux dire, on s’attend à ce que le cuir de Lamborghini soit cousu à la main. Mais ces ailes et ces guêtres à l’allure aérospatiale, le gros tube de carbone au cœur de l’Aventador ? On dirait que tout cela a été conçu à partir d’un vaisseau d’atterrissage extraterrestre capturé, et non pas fabriqué à la main par une Italienne nommée Piera. Et pourtant, c’est toujours le moyen le plus économique de produire de la fibre de carbone. A petite échelle, en tout cas.
« Si je dois faire dix pièces, le fait main reste le meilleur moyen », déclare Luciano De Oto, responsable du centre de recherche avancée sur les composites de Lamborghini. « Au-delà de 2 000 pièces, je dois augmenter l’automatisation et utiliser de la fibre coupée ». Ce serait de la fibre de carbone « forgée », mais nous y reviendrons. D’abord, je dois emballer ma pièce sous vide.
Pour que la première couche de fibre de carbone se conforme au moule, je scelle la feuille dans du plastique et j’aspire toutes les poches d’air entre les couches. Ensuite, je recouvre le tout d’un tissu plus lourd avant de placer le tout dans un autre sac à vide en plastique plus épais, du genre de ceux que vous utiliseriez pour rétrécir votre couette pour la ranger en été. Après avoir éliminé l’air emprisonné, nous mettons quatre autres couches, puis une autre routine de mise sous vide après la dernière couche. C’est fastidieux. Des entreprises comme BMW construisent des lignes de production robotisées pour le faire plus rapidement que les humains. Mais même dans ce cas, c’est lent.
En plus d’être gourmand en temps, le processus de fabrication de la fibre de carbone est aussi un gros consommateur d’énergie. Les congélateurs de stockage et le souffle occasionnel du sèche-cheveux sont mineurs comparés à l’autoclave, un four pressurisé utilisé pour durcir les pièces finies. Le morceau de tissu que j’ai déposé à la main va cuire dans le four pendant six heures à près de 400 degrés, le tout sous une pression six fois supérieure à la pression atmosphérique normale. Au moins Lamborghini a un panneau solaire photoélectrique de 1,2 mégawatt sur le toit de l’usine.
Une solution de production de masse
Pendant que mon composant se prépare, je me dirige vers la zone où Lamborghini fabrique des pièces forgées. Au lieu du pré-imprégné soigneusement tissé avec lequel j’ai travaillé plus tôt, les machines utilisent ici une fibre de carbone brute connue sous le nom de chopped mat. Un carré de ce matériau est pressé en formes de base sur un moule, puis déplacé dans la forge à huit pistons, qui applique une chaleur de 300 degrés et une pression de 2 900 psi. Contrairement au pré-imprégné, le chopped mat peut être écrasé en formes exotiques – ancres de vis, fines crêtes – qui ne sont pas possibles lorsque vous emballez du tissu à la main. Le processus est en grande partie automatisé, et en 20 minutes nous aurons la même pièce qui a encore besoin d’environ cinq heures dans l’autoclave.
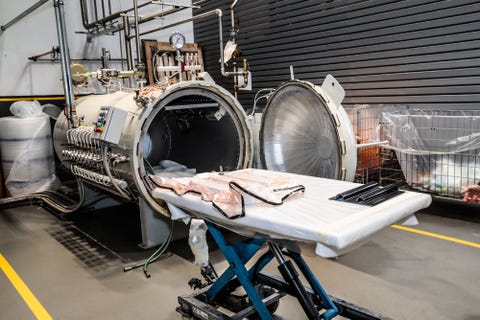
Un produit forgé n’est pas aussi léger ou solide que le produit posé à la main, mais si la fibre de carbone doit un jour être généralisée, cela semble être la voie à suivre. « Les diamants ont un coût plus élevé que l’or », dit De Oto. « La fibre de carbone posée à la main n’atteindra pas le coût de l’aluminium, mais dans les dix prochaines années, le mat haché pourrait le faire. » Même si les voitures ne sont équipées que de la fibre de carbone hachée, comme c’est le cas pour la BMW i3, il s’agit d’une amélioration considérable par rapport à l’aluminium. Plus léger, plus de mpg, et aucune sécurité perdue.
Mais les trucs sophistiqués posés à la main, avec ses congélateurs et ses autoclaves, ses sacs sous vide et ses raclettes et ses moules fragiles ? Ce sera toujours un matériau exotique pour les voitures exotiques. Lamborghini a besoin de trois semaines pour produire chaque carrosserie blanche d’Aventador. Cette cadence ne sera jamais atteinte à l’usine Accord de l’Ohio.
À 17 heures, l’usine se vide, et je rejoins les ouvriers en blouse noire qui s’écoulent par la porte. Je ne verrai jamais la pièce que j’ai fabriquée. Elle est toujours dans l’autoclave, et je n’ai pas le temps d’attendre.
Faits sur les fibres de carbone
Thomas Edison a fabriqué des fibres de carbone à partir de bambou et de coton, les utilisant comme filaments dans les ampoules.
Boeing peut réparer des dommages mineurs aux composites de carbone du 787 à la porte d’embarquement, en moins d’une heure.
Environ 70 % de la fibre de carbone est produite par le Japon.
La chose la plus stupide faite en fibre de carbone : le fedora en fibre de carbone.
Les docteurs volants
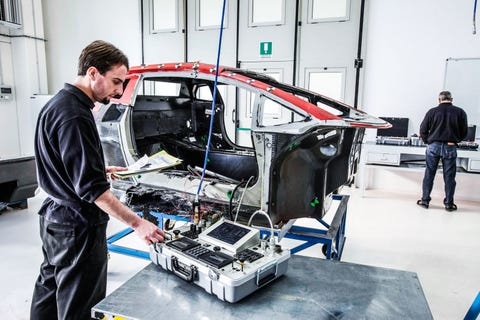
Lorsqu’une Aventador s’écrase, Lamborghini envoie les docteurs volants, des techniciens formés pour réparer les pièces en fibre de carbone. L’équipe garde six malles à vapeur surdimensionnées avec des équipements à ultrasons et des machines de durcissement portables positionnées stratégiquement dans le monde entier. Pourquoi ne pas les enregistrer avec leurs bagages ? « Les douanes n’aiment pas avoir affaire à des produits chimiques », explique Casper Steenbergen, responsable de la réparation des matériaux en fibre de carbone. En outre, pas besoin de délais supplémentaires. « Nous avons dû fabriquer de nouveaux gabarits pour une section entière de panneau de bas de caisse pour une voiture en Chine », dit-il. « Cette réparation a pris deux semaines ». Les techniciens excisent la section endommagée et reconstruisent, couche par couche, jusqu’à ce que la fibre de carbone soit certifiée conforme aux spécifications d’origine. En fait, Lamborghini a rédigé la norme ISO 17065, ce qui signifie que Ferrari doit suivre les règles de Lamborghini pour certifier la réparation d’une Enzo cassée. Et oui, les docteurs volants ont l’air d’en prendre plein la vue.
Cette histoire apparaît dans le Popular Mechanics de mars 2017.
.