Proč jsou uhlíková vlákna zázračným materiálem
Uhlíková vlákna, která jsou pevnější než ocel a mají zlomek hmotnosti, jsou geniálním vynálezem. Je jím už desítky let. Junior Johnson z něj v 80. letech stavěl závodní vozy Nascar překračující pravidla. Ale i když se za tu dobu podařilo vymyslet nové zdroje a výrobní postupy, uhlíková vlákna prostě nepřestanou být drahá. Nejlevnější nový vůz s karbonovou karoserií, Alfa Romeo 4C, je velký jako Stuart Little, ale stojí stejně jako Mercedes třídy E. A skutečné vozy karbonových bohů, McLareny, Koenigseggy a Lamborghini Aventadory, jsou přísně šestimístné. Stále se nám nepodařilo masově vyrábět tento materiál za cenu blížící se ceně hliníku, natož oceli. Proč ještě nikdo nepřišel na to, jak to vyrobit levněji?
Tato otázka je důvodem, proč jsem tady v Sant’Agata Bolognese v Itálii, v závodě Lamborghini na výrobu uhlíkových vláken, a pracně vymačkávám vzduchové bubliny z plátu uhlíkové vazby. Chci se zeptat chlapů v (černých) laboratorních pláštích, kteří tento materiál vyrábějí: Proč se nevozíme v Hyundaie s karbonovým monokokem?
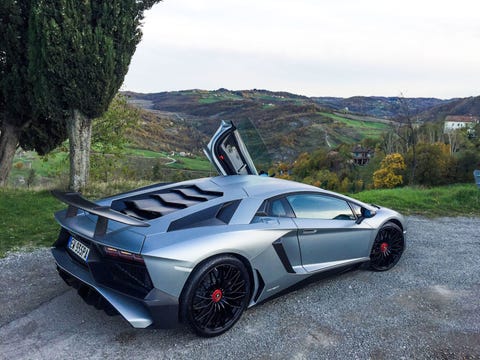
Uhlík vs. ocel
V roce 2017 se pro vytvoření kovových součástí, které tvoří jádro většiny aut, nalije superžhavý tekutý hliník, ocel nebo hořčík do formy a odlije. Můžete ji rozbít do tvaru, můžete ji vyřezat pomocí CNC stroje, můžete kusy svařit dohromady. Máte možnosti, všechny jsou poměrně rychlé a cenově dostupné. Chcete-li vyrobit díl z uhlíkových vláken… no, nejprve musíte vyndat surovinu z mrazáku.
Lesklé tkané role uhlíkových vláken, naplněné pryskyřicí (tzv. pre-preg) a podložené lepidlem, se skladují při teplotě nula stupňů Fahrenheita. Pokud bude tepleji, pryskyřice ztvrdne. Tato citlivost na teplotu také znamená, že materiál nemůžete řezat do tvaru pomocí CNC laseru – abyste ho udrželi chladný a poddajný, musíte použít nůž, který se časem opotřebuje. I pak ale čas běží. Od okamžiku, kdy je vyříznuto první vlákno těchto plastových uhlíkových vláken, máte na jeho vytvarování přibližně jeden den.
Takže si pospíšíte s plastovými špachtlemi a černostříbrné pláty vtlačíte do formy, která vydrží jen asi 300 použití, než se zdeformuje a vyhodí do popelnice. Piera, žena, která má za úkol mi to všechno vysvětlit, se zdá být zmatená mým hlemýždím tempem. Přináší fén a zahřívá materiál, aby byl poddajnější. Ale samozřejmě nechcete příliš velké teplo, aby se váš prepreg předčasně nezkalcifikoval do nesprávného tvaru.
Futuristické, ale ručně vyrobené
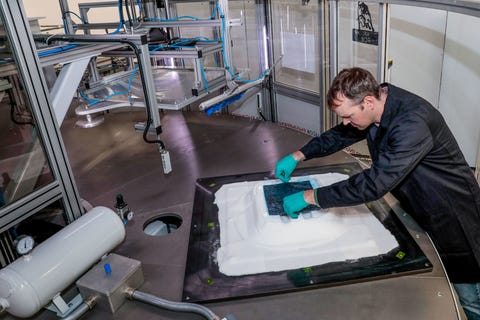
Asi před deseti lety jsem navštívil další z továren Lamborghini. Sledoval jsem ženu, která s láskou sešívala sedadla na Murciélagu a praktikovala metodické řemeslo, které by bylo pro masově prodávaný vůz příliš pracné a neefektivní. Teď jsem tu znovu a jsem svědkem podobného stupně ruční umělecké práce vložené do tvorby materiálu, který považujeme za mnohem futurističtější. Člověk by přece čekal, že kůže Lamborghini byla šitá ručně. Ale ta letecky vypadající křídla a blatníky, ta velká karbonová vana v srdci Aventadoru? To všechno vypadá, jako by to bylo zpětně sestrojeno ze zachyceného mimozemského přistávacího plavidla, a ne ručně vyrobeno Italkou jménem Piera. A přesto je to stále nejekonomičtější způsob výroby uhlíkových vláken. Alespoň v malém měřítku.
„Pokud mám udělat deset dílů, ruční výroba je stále nejlepší způsob,“ říká Luciano De Oto, šéf Centra pokročilého kompozitního výzkumu Lamborghini. „Nad dva tisíce dílů musím zvýšit automatizaci a používat sekaná vlákna.“ To by byla „kovaná“ uhlíková vlákna, ale k tomu se ještě dostaneme. Nejprve musím svůj díl vakuově zabalit.
Abych zajistil, že se první vrstva uhlíkových vláken přizpůsobí formě, utěsním list v plastu a vysajeme případné vzduchové kapsy mezi vrstvami. Pak to přikryji těžší látkou a teprve potom to celé vložím do dalšího silnějšího plastového vakuového sáčku, takového, jaký se používá na smršťování peřin pro letní skladování. Po odstranění zachyceného vzduchu nastavíme další čtyři vrstvy, pak ještě jednu vakuovou rutinu po poslední vrstvě. Je to zdlouhavé. Společnosti jako BMW staví robotické výrobní linky, aby to zvládly rychleji než lidé. Ale i tak je to pomalé.
Kromě časové náročnosti je proces výroby uhlíkových vláken také energeticky náročný. Skladovací mrazáky a občasný výbuch fénem jsou zanedbatelné ve srovnání s autoklávem, tlakovou pecí používanou k vytvrzování hotových dílů. Můj konkrétní kus ručně vyráběné dobroty se v ní peče šest hodin při teplotě téměř 400 stupňů, a to vše pod šestinásobkem běžného atmosférického tlaku. Lamborghini má na střeše továrny alespoň 1,2megawattové fotoelektrické solární pole.
Řešení pro hromadnou výrobu
Když se moje součástka šetří, zamířím do oblasti, kde Lamborghini vyrábí kované díly. Místo úhledně tkaného prepregu, se kterým jsem pracoval dříve, zde stroje používají hrubé uhlíkové vlákno známé jako sekaná rohož. Čtverec tohoto materiálu se lisuje do základních tvarů přes formu a pak se přesune do osmipístové kovárny, která působí teplem 300 stupňů a tlakem 2 900 psi. Na rozdíl od prepregu lze sekanou rohož roztlačit do exotických tvarů – šroubových kotev, tenkých hřebenů -, což při ručním ovíjení látky není možné. Proces je většinou automatizovaný a za 20 minut máme stejný díl, který ještě potřebuje asi pět hodin v autoklávu.
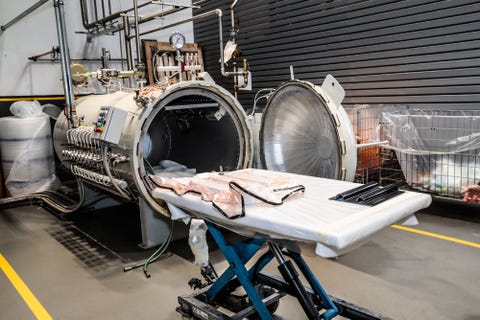
Kovaný výrobek není tak lehký ani pevný jako ručně ovinutý materiál, ale pokud se mají karbonová vlákna někdy dostat do hlavního proudu, tohle vypadá jako cesta. „Diamanty mají vyšší cenu než zlato,“ říká De Oto. „Ručně kladená uhlíková vlákna nedosáhnou ceny hliníku, ale v příštích deseti letech by to mohla být sekaná rohož.“ I kdyby automobily dostávaly jen sekané rohože z uhlíkových vláken, jako je tomu u BMW i3, stále je to obrovský pokrok oproti hliníku. Je lehčí, má vyšší spotřebu a neztrácí na bezpečnosti.
Ale sofistikované ručně kladené materiály s jejich mrazáky a autoklávy, vakuovými sáčky a stěrkami a křehkými formami? To bude vždycky exotický materiál pro exotická auta. Lamborghini potřebuje na výrobu každé bílé karoserie Aventadoru tři týdny. Takové tempo se v továrně Accord v Ohiu nikdy nestihne.
V 17:00 se továrna vyklízí a já se přidávám k dělníkům v černých laboratorních pláštích proudícím branou. Díl, který jsem vyrobil, nikdy neuvidím. Je stále v autoklávu a já nemám čas čekat.“
Fakta o uhlíkových vláknech
Thomas Edison vyrobil uhlíková vlákna z bambusu a bavlny a používal je jako vlákna v žárovkách.
Boeing dokáže opravit drobná poškození uhlíkových kompozitů letounu 787 přímo u brány, a to za méně než hodinu.
Přibližně 70 procent uhlíkových vláken se vyrábí v Japonsku.
Nejhloupější věc vyrobená z uhlíkových vláken: karbonová fedora.
Létající doktoři
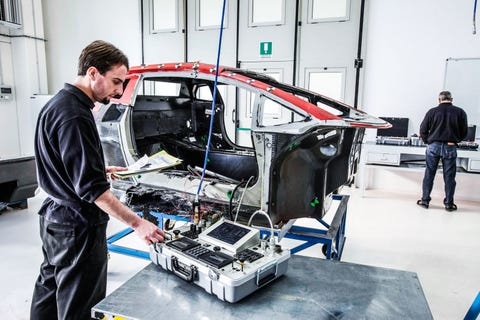
Když Aventador havaruje, Lamborghini vyšle létající doktory, techniky vyškolené na opravu dílů z uhlíkových vláken. Tým má po celém světě strategicky rozmístěno šest nadrozměrných parních kufrů s ultrazvukovým zařízením a přenosnými vytvrzovacími stroji. Proč je nezkontrolovat spolu s jejich zavazadly? „Celníci neradi pracují s chemikáliemi,“ říká Casper Steenbergen, vedoucí oddělení oprav materiálů z uhlíkových vláken. Kromě toho není třeba dalších zdržení. „Museli jsme v Číně vyrobit nové přípravky na celou část kyvné desky pro jedno auto,“ říká. „Tato oprava trvala dva týdny.“ Technici vyříznou poškozenou část a znovu ji postaví, vrstvu po vrstvě, dokud nejsou karbonová vlákna certifikována podle původní specifikace. Lamborghini vlastně napsalo normu ISO 17065, což znamená, že Ferrari musí při certifikaci opravy poškozeného Enza dodržovat pravidla Lamborghini. A ano, zdá se, že létající lékaři z toho mají radost.
Tento příběh vyšel v časopise Popular Mechanics v březnu 2017.
.