Varför kolfiber är ett mirakelmaterial
Kolfiber är en lysande uppfinning, starkare än stål och en bråkdel av vikten. Har varit det i årtionden. Junior Johnson byggde regelbrytande Nascar-racers av materialet på 80-talet. Men trots all den tid som gått åt till att komma på nya inköp och produktionsmetoder slutar kolfiber bara inte att vara dyrt. Den billigaste nya bilen med en karbonfiberkaross, Alfa Romeo 4C, är stor nog för Stuart Little, men kostar lika mycket som en Mercedes E-klass. Och kolgudarnas verkliga vagnar, världens McLarens, Koenigseggs och Lamborghini Aventadors, är strikt sexsiffriga förslag. Vi har fortfarande inte lyckats massproducera materialet till ett pris som närmar sig priset för aluminium, för att inte tala om stål. Varför har ingen kommit på hur man kan få det här att kosta mindre?
Den frågan är anledningen till att jag är här i Sant’Agata Bolognese, Italien, på Lamborghinis kolfiberanläggning, där jag mödosamt skrapar ut luftbubblor ur ett ark med kolfiberväv. Jag vill fråga killarna i (svarta) labbrockar som tillverkar detta material: Varför rullar vi inte runt i Hyundais med kolmonocoque?
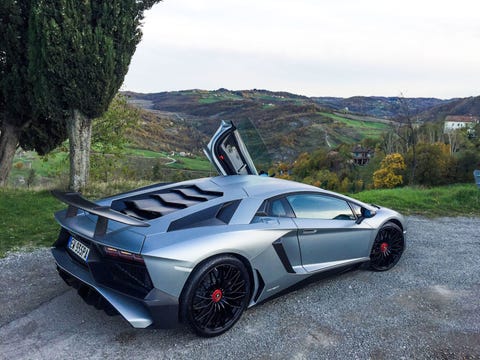
Kol vs stål
Inför 2017, för att skapa metallkomponenterna i kärnan av de flesta bilar, häller du din supervarma flytande aluminium, stål eller magnesium i en gjutform och gjuter det. Du kan krossa den i form, du kan snida den med en CNC-maskin, du kan svetsa ihop delar. Det finns många alternativ, och alla är relativt snabba och prisvärda. För att tillverka en del av kolfiber … ja, först måste man hämta ut råmaterialet ur frysen.
De glänsande vävda rullarna av kolfiber, fyllda med harts (så kallad pre-preg) och backade med lim, förvaras vid noll grader Fahrenheit. Om det är varmare kommer hartset att hårdna. Denna temperaturkänslighet innebär också att man inte kan skära materialet i form med en CNC-laser – för att hålla det kallt och formbart måste man använda en kniv, som så småningom slits ut. Även då är klockan tickande. Från det att den första väven av dessa plastkoltrådar skärs har du ungefär en dag på dig att forma den.
Så du skyndar dig med plastspatlarna och tvingar in de svarta och silverfärgade arken i en form, som bara håller för cirka 300 användningar innan den deformeras och slängs. Piera, kvinnan som har till uppgift att förklara allt detta för mig, verkar förbryllad över min långsamma takt. Hon tar fram en hårtork och värmer upp materialet för att göra det mer följsamt. Men man vill förstås inte ha för mycket värme, för att inte prepregs ska förkalkas i förtid och få fel form.
Futuristiskt men hantverksmässigt
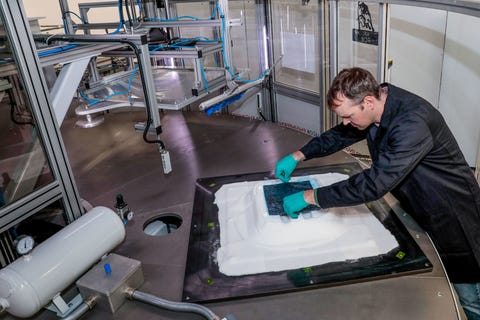
För ungefär ett decennium sedan besökte jag en annan av Lamborghinis anläggningar. Jag såg en kvinna som kärleksfullt sydde sätena på en Murciélago och praktiserade ett slags metodiskt hantverk som skulle vara för mödosamt, för ineffektivt för en bil för massmarknaden. Nu är jag här igen och bevittnar en liknande grad av manuell konstnärlighet som investeras i skapandet av ett material som vi anser vara mycket mer futuristiskt. Jag menar, man kan förvänta sig att Lamborghinis läder sys för hand. Men de där flygplansliknande vingarna och spatarna, det stora kolröret i hjärtat av Aventador? Allt ser ut som om det har konstruerats från en fångad utomjordisk landningsfarkost, inte handgjord av en italiensk kvinna vid namn Piera. Ändå är detta fortfarande det mest ekonomiska sättet att tillverka kolfiber. I liten skala i alla fall.
”Om jag måste göra tio delar är handgjord fortfarande det bästa sättet”, säger Luciano De Oto, chef för Lamborghinis Advanced Composite Research Center. ”Över 2 000 delar måste jag öka automatiseringen och använda hackad fiber.” Det skulle vara ”smidd” kolfiber, men det ska vi komma till. Först måste jag vakuumförpacka min del.
För att säkerställa att det första lagret kolfiber följer formen förseglar jag arket i plast och suger ut eventuella luftfickor mellan lagren. Sedan täcker jag det med en tyngre trasa innan jag placerar det hela i en annan tjockare plastvakuumpåse, den sorten som du använder för att krympa ditt täcke för sommarförvaring. Efter att ha avlägsnat instängd luft sätter vi fyra lager till, och sedan ytterligare en vakuumrutin efter det sista lagret. Det är tråkigt. Företag som BMW bygger robotiserade produktionslinjer för att göra detta snabbare än människor. Men även då är det långsamt.
Förutom att vara tidskrävande är kolfibertillverkningsprocessen också en energislukare. Förvaringsfrysarna och tillfälliga stötar med hårtorken är små i jämförelse med autoklaven, en trycksatt ugn som används för att härda de färdiga delarna. Min speciella bit av handgjord godhet kommer att gräddas i ugnen i sex timmar vid nästan 400 grader, samtidigt som den står under sex gånger det normala atmosfäriska trycket. Lamborghini har åtminstone en 1,2 megawatt fotoelektrisk solcellsanläggning på fabrikens tak.
En massproduktionslösning
Medan min komponent förbereds går jag till det område där Lamborghini tillverkar smidda delar. I stället för den prydligt vävda prepreg som jag arbetade med tidigare använder maskinerna här en grov kolfiber som kallas chopped mat. En kvadrat av detta material pressas till grundläggande former över en form och flyttas sedan in i den åttakolviga smedjan, som tillämpar 300 graders värme och ett tryck på 2 900 psi. Till skillnad från prepreg kan hackad matta pressas till exotiska former – skruvförankringar, tunna kammar – som inte är möjliga när man lindar in tyg för hand. Processen är mestadels automatiserad, och på 20 minuter har vi samma del som fortfarande behöver fem timmar till i autoklaven.
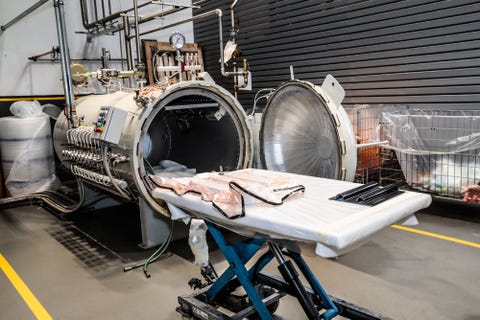
En smidd produkt är inte lika lätt eller stark som de handlagda sakerna, men om kolfiber någonsin kommer att bli mainstream ser detta ut att vara vägen. ”Diamanter har en högre kostnad än guld”, säger De Oto. ”Handlagd kolfiber kommer inte att nå upp till kostnaden för aluminium, men inom de närmaste tio åren kan hackad matta komma att bli det.” Även om bilarna bara får kolfiber med hackad matta, som på BMW i3, är det ändå en enorm uppgradering från aluminium. Lättare, mer bränsle och ingen förlorad säkerhet.
Men de sofistikerade handgjorda materialen, med frysar och autoklaver, vakuumpåsar, skrapor och ömtåliga formar? Det kommer alltid att vara ett exotiskt material för exotiska bilar. Lamborghini behöver tre veckor för att tillverka varje Aventador-kaross i vitt. Den takten kommer aldrig att hålla i Accord-fabriken i Ohio.
Vid 17:00 håller fabriken på att rensas ut, och jag ansluter mig till arbetarna i svarta labbrockar som flödar genom porten. Jag får aldrig se den del som jag tillverkade. Den är fortfarande i autoklaven och jag har inte tid att vänta.
Kolfiberfakta
Thomas Edison tillverkade kolfiber av bambu och bomull och använde dem som glödtråd i glödlampor.
Boeing kan reparera mindre skador på 787:ans kolkompositer vid gaten, på mindre än en timme.
Omkring 70 procent av kolfibern tillverkas av Japan.
Det dummaste som är tillverkat av kolfiber: kolfiberfodralet.
De flygande läkarna
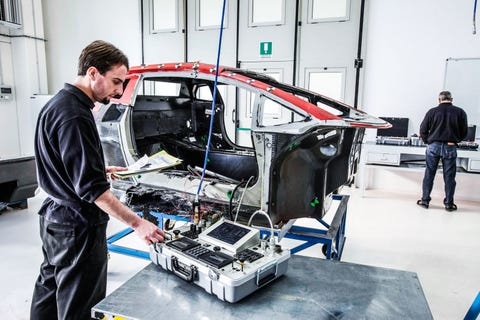
När en Aventador kraschar skickar Lamborghini ut de flygande läkarna, tekniker som är utbildade för att reparera kolfiberdelar. Teamet har sex överdimensionerade ångbåtar med ultraljudsutrustning och bärbara härdningsmaskiner strategiskt placerade runt om i världen. Varför inte checka in den med sitt bagage? ”Tullen gillar inte att hantera kemikalier”, säger Casper Steenbergen, chef för reparation av kolfibermaterial. Dessutom behövs inga ytterligare förseningar. ”Vi var tvungna att göra nya jiggar för en hel sektion av en gungbräda till en bil i Kina”, säger han. ”Den reparationen tog två veckor.” Teknikerna tar bort den skadade sektionen och bygger upp den igen, lager för lager, tills kolfibern är certifierad enligt de ursprungliga specifikationerna. Faktum är att Lamborghini skrev standarden, ISO 17065, vilket innebär att Ferrari måste följa Lamborghinis regler för att certifiera reparationen av en trasig Enzo. Och ja, de flygande läkarna verkar få en kick av detta.
Denna berättelse finns i Popular Mechanics från mars 2017.
.