Waarom koolstofvezel het wondermateriaal is
Steviger dan staal en een fractie van het gewicht, koolstofvezel is een briljante uitvinding. Dat is het al tientallen jaren. Junior Johnson bouwde in de jaren ’80 al Nascar-racers van dit materiaal die de regels overtraden. Maar zelfs met al die tijd om nieuwe inkoop- en productiemethoden te bedenken, blijft koolstofvezel gewoon duur. De goedkoopste nieuwe auto met een koolstofvezel kuip, de Alfa Romeo 4C, is zo groot als Stuart Little, maar kost evenveel als een Mercedes E-Klasse. En de echte strijdwagens van de koolstofgoden, de McLarens en Koenigseggs en Lamborghini Aventadors van de wereld, kosten maar liefst zes cijfers. We zijn er nog steeds niet in geslaagd om het spul in massa te produceren tegen een prijs die ook maar in de buurt komt van die van aluminium, laat staan staal. Waarom heeft niemand bedacht hoe we dit spul goedkoper kunnen maken?
Die vraag is waarom ik hier ben in Sant’Agata Bolognese, Italië, in Lamborghini’s koolstofvezel faciliteit, moeizaam persen van luchtbellen uit een vel van koolstofweefsel. Ik wil de jongens in (zwarte) laboratoriumjassen die dit materiaal maken vragen: Waarom rollen we niet rond in carbon-monocoque Hyundais?
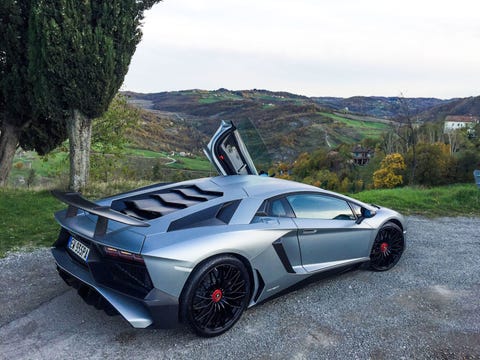
Carbon vs. Steel
In 2017, om de metalen onderdelen te maken die de kern vormen van de meeste auto’s, giet je je superhete vloeibare aluminium of staal of magnesium in een mal, en giet je het. Je kunt het in vorm slaan, je kunt het snijden met een CNC machine, je kunt stukken aan elkaar lassen. Je hebt opties, allemaal redelijk snel en betaalbaar. Om een onderdeel van koolstofvezel te maken… moet je eerst de grondstof uit de vriezer halen.
De glanzende geweven rollen koolstofvezel, gevuld met hars (pre-preg genoemd) en voorzien van lijm, worden opgeslagen bij nul graden Fahrenheit. Elke warmer en de hars zal verharden. Die temperatuurgevoeligheid betekent ook dat je het materiaal niet in vorm kunt snijden met een CNC-laser – om het koel en buigzaam te houden, moet je een mes gebruiken, dat uiteindelijk slijt. En zelfs dan tikt de klok door. Vanaf het moment dat het eerste weefsel van deze plastic koolstofdraden is gesneden, heb je ongeveer een dag om het vorm te geven.
Dus haast je je met de plastic spatels en dwingt de zwarte en zilveren vellen in een mal, die slechts goed zal zijn voor ongeveer 300 toepassingen voordat hij vervormd is en wordt weggegooid. Piera, de vrouw die mij dit alles moet uitleggen, lijkt verbijsterd over mijn ploetertempo. Ze haalt een haardroger te voorschijn en verwarmt het materiaal om het plooibaarder te maken. Maar je wilt natuurlijk niet te veel warmte, anders verkalkt je pre-preg voortijdig in de verkeerde vorm.
Futuristisch maar handgemaakt
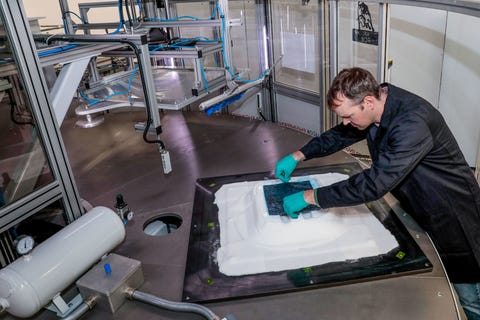
Ongeveer tien jaar geleden bezocht ik een van de fabrieken van Lamborghini. Ik zag hoe een vrouw liefdevol de stoelen van een Murciélago naaide, een soort methodisch vakmanschap dat te omslachtig en te inefficiënt zou zijn voor een auto voor de massamarkt. Nu ben ik hier opnieuw getuige van een vergelijkbare mate van handwerk en kunstzinnigheid bij de creatie van een materiaal dat wij als veel futuristischer beschouwen. Ik bedoel, je zou verwachten dat Lamborghini’s leer met de hand gestikt is. Maar die vleugels en spatborden, de grote koolstof buis in het hart van de Aventador? Het ziet er allemaal uit alsof het is overgenomen van een buitgemaakt buitenaards landingsvaartuig, niet met de hand gemaakt door een Italiaanse vrouw genaamd Piera. En toch, is dit nog steeds de meest economische manier om koolstofvezel te produceren. Op kleine schaal, in ieder geval.
“Als ik tien onderdelen moet maken, is handgemaakt nog steeds de beste manier,” zegt Luciano De Oto, hoofd van Lamborghini’s Advanced Composite Research Center. “Boven de 2.000 onderdelen, moet ik de automatisering verhogen en gehakte vezels gebruiken.” Dat zou “gesmede” koolstofvezel zijn, maar daar komen we zo op. Eerst, moet ik mijn onderdeel vacuüm verpakken.
Om er zeker van te zijn dat de eerste laag koolstofvezel zich aan de mal aanpast, sluit ik de plaat af met plastic en zuig eventuele luchtbellen tussen de lagen weg. Dan bedek ik dat met een zwaardere doek voordat ik het geheel in een andere dikkere plastic vacuümzak stop, van het soort dat je gebruikt om je dekbed in te krimpen voor de zomeropslag. Nadat de ingesloten lucht is verwijderd, leggen we nog vier lagen, en na de laatste laag nog een vacuüm routine. Het is eentonig. Bedrijven als BMW bouwen robot productielijnen om dit sneller te doen dan mensen. Maar zelfs dan, het is traag.
Naast tijdsintensief, is het koolstofvezel productieproces ook een energievreter. De vriezers voor opslag en af en toe een föhnbeurt zijn van ondergeschikt belang vergeleken met de autoclaaf, een oven onder druk die wordt gebruikt om afgewerkte onderdelen uit te harden. Mijn specifieke brok handgelegde goedheid zal zes uur lang in de oven bakken bij bijna 400 graden, en dat alles onder zes keer de normale atmosferische druk. Lamborghini heeft tenminste een 1.2-megawatt foto-elektrisch zonnepaneel op het dak van de fabriek.
Een massaproduktie-oplossing
Terwijl mijn onderdelen worden gekoeld, ga ik naar het gebied waar Lamborghini gesmede onderdelen maakt. In plaats van de netjes geweven pre-preg waar ik eerder mee werkte, gebruiken de machines hier een ruwe koolstofvezel die bekend staat als chopped mat. Een vierkant van dit materiaal wordt boven een mal in basisvormen geperst en dan in de smederij met acht zuigers gebracht, waar hitte van 300 graden en een druk van 2.900 psi wordt toegepast. In tegenstelling tot pre-preg kan chopped mat in exotische vormen worden geperst – schroefankers, dunne richels – die niet mogelijk zijn wanneer stof met de hand wordt gewikkeld. Het proces is grotendeels geautomatiseerd, en in 20 minuten hebben we hetzelfde onderdeel dat nog ongeveer vijf uur in de autoclaaf moet.
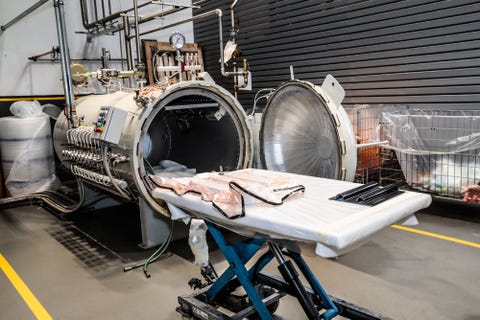
Een gesmeed product is niet zo licht of sterk als het met de hand gelegde spul, maar als koolstofvezel ooit mainstream gaat worden, lijkt dit de manier te zijn. “Diamanten zijn duurder dan goud,” zegt De Oto. “Hand gelegd koolstofvezel zal niet de kosten van aluminium te bereiken, maar in de komende tien jaar, gehakte mat misschien wel.” Zelfs als auto’s alleen koolstofvezel krijgen, zoals in de BMW i3, is dat nog steeds een enorme upgrade ten opzichte van aluminium. Lichter, meer mpg, en geen verlies van veiligheid.
Maar het geavanceerde handgemaakte spul, met zijn vriezers en autoclaven, vacuümzakken en knijpers en fragiele mallen? Dat zal altijd een exotisch materiaal blijven voor exotische auto’s. Lamborghini heeft drie weken nodig om elke Aventador body-in-white te produceren. Dat tempo zal nooit vliegen in de Accord fabriek in Ohio.
Tegen 17:00, is de fabriek aan het opruimen, en ik voeg me bij de arbeiders in zwarte labo jassen die door de poort stromen. Ik zie nooit het onderdeel dat ik gemaakt heb. Het ligt nog in de autoclaaf, en ik heb geen tijd om te wachten.
Koolstofvezelfeiten
Thomas Edison maakte koolstofvezels van bamboe en katoen, en gebruikte ze als gloeidraad in gloeilampen.
Boeing kan kleine beschadigingen aan de koolstofcomposieten van de 787 aan de poort repareren, in minder dan een uur.
Ongeveer 70 procent van de koolstofvezel wordt geproduceerd door Japan.
Domste ding gemaakt van koolstofvezel: de koolstofvezel fedora.
De Flying Doctors
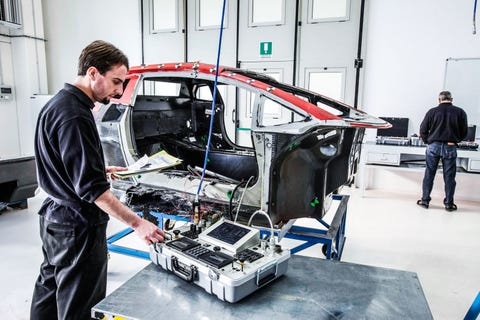
Als een Aventador crasht, stuurt Lamborghini de Flying Doctors op pad, technici die zijn opgeleid om koolstofvezel onderdelen te repareren. Het team beschikt over zes oversized stoomkoffers met ultrasone apparatuur en draagbare hardingsmachines die strategisch over de hele wereld zijn gepositioneerd. Waarom die niet met hun bagage inchecken? “De douane houdt niet van chemicaliën”, zegt Casper Steenbergen, hoofd reparatie van koolstofvezel materialen. Bovendien is er geen behoefte aan extra oponthoud. “We moesten nieuwe mallen maken voor een heel tuimelpaneel voor een auto in China”, zegt hij. “Die reparatie duurde twee weken.” Technici halen het beschadigde deel eruit en bouwen het opnieuw op, laag voor laag, totdat de koolstofvezel gecertificeerd is volgens de oorspronkelijke specificaties. In feite schreef Lamborghini de standaard, ISO 17065, wat betekent dat Ferrari Lamborghini’s regels moet volgen om de reparatie van een kapotte Enzo te certificeren. En ja, de Flying Doctors schijnen daar een kick van te krijgen.
Dit verhaal verschijnt in de Popular Mechanics van maart 2017.